Fórmula geral da estrutura da matriz de rosqueamento
Para roscas de tamanho pequeno, um punção é geralmente usado em matrizes de rosqueamento, enquanto para roscas maiores (M5 e superiores), um punção com furo pré-fabricado é comumente empregado, permitindo que a punção e o rosqueamento sejam concluídos de uma só vez.
Quando o punção desce até uma altura definida, o material é rasgado sob a ação da aresta de corte plana. Na maioria dos casos, o material residual do processo de puncionamento permanece preso após o rosqueamento, mas se soltará sozinho após o rosqueamento, conforme mostrado na Figura 5-20.
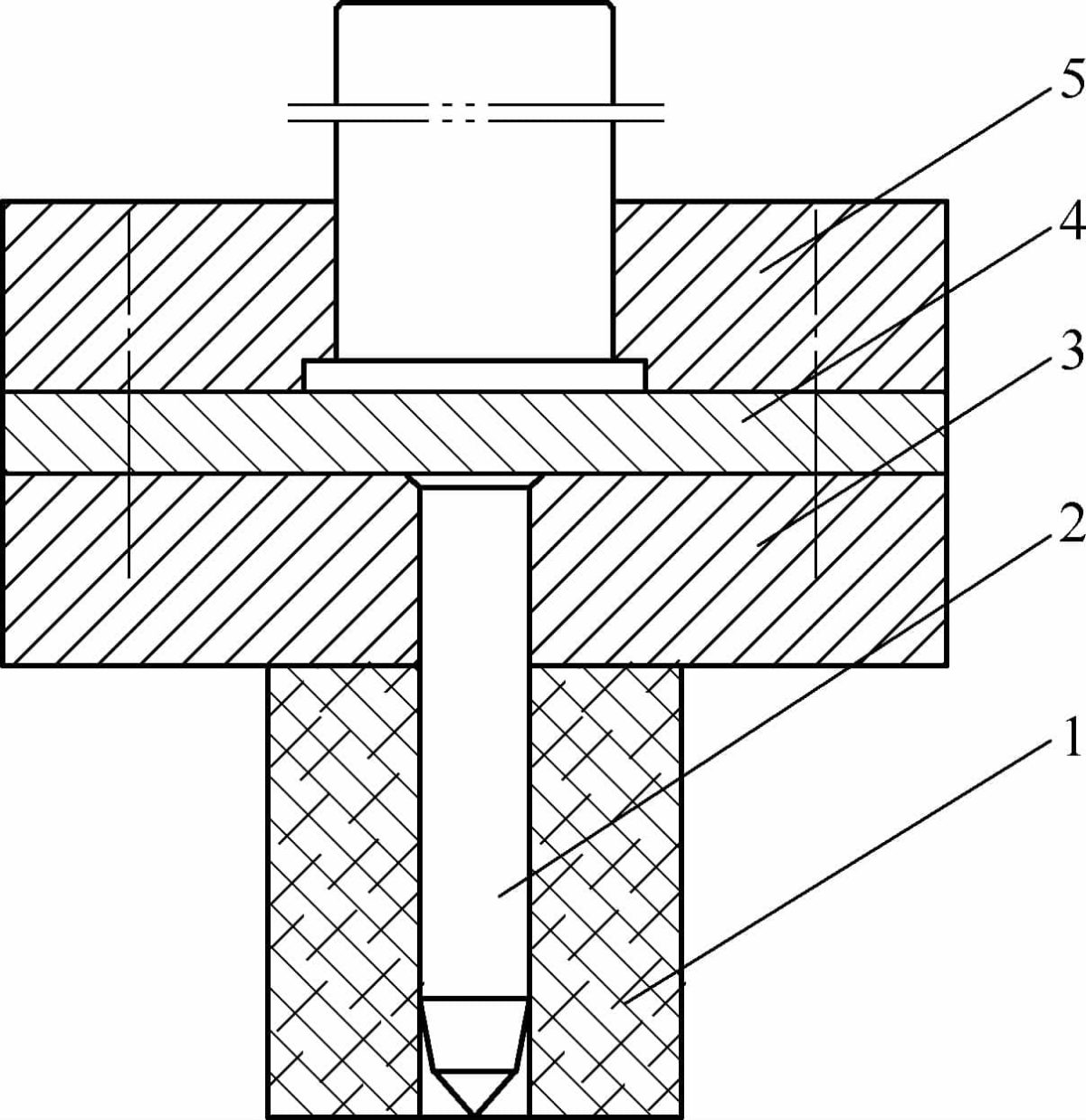
1—Elastômero de borracha 2—Punção 3—Placa de retenção do punção 4—Placa de apoio 5—Suporte superior da matriz
Ao flangear vários furos simultaneamente na matriz secundária, devem ser instalados postes-guia e buchas, conforme ilustrado na Figura 5-21.
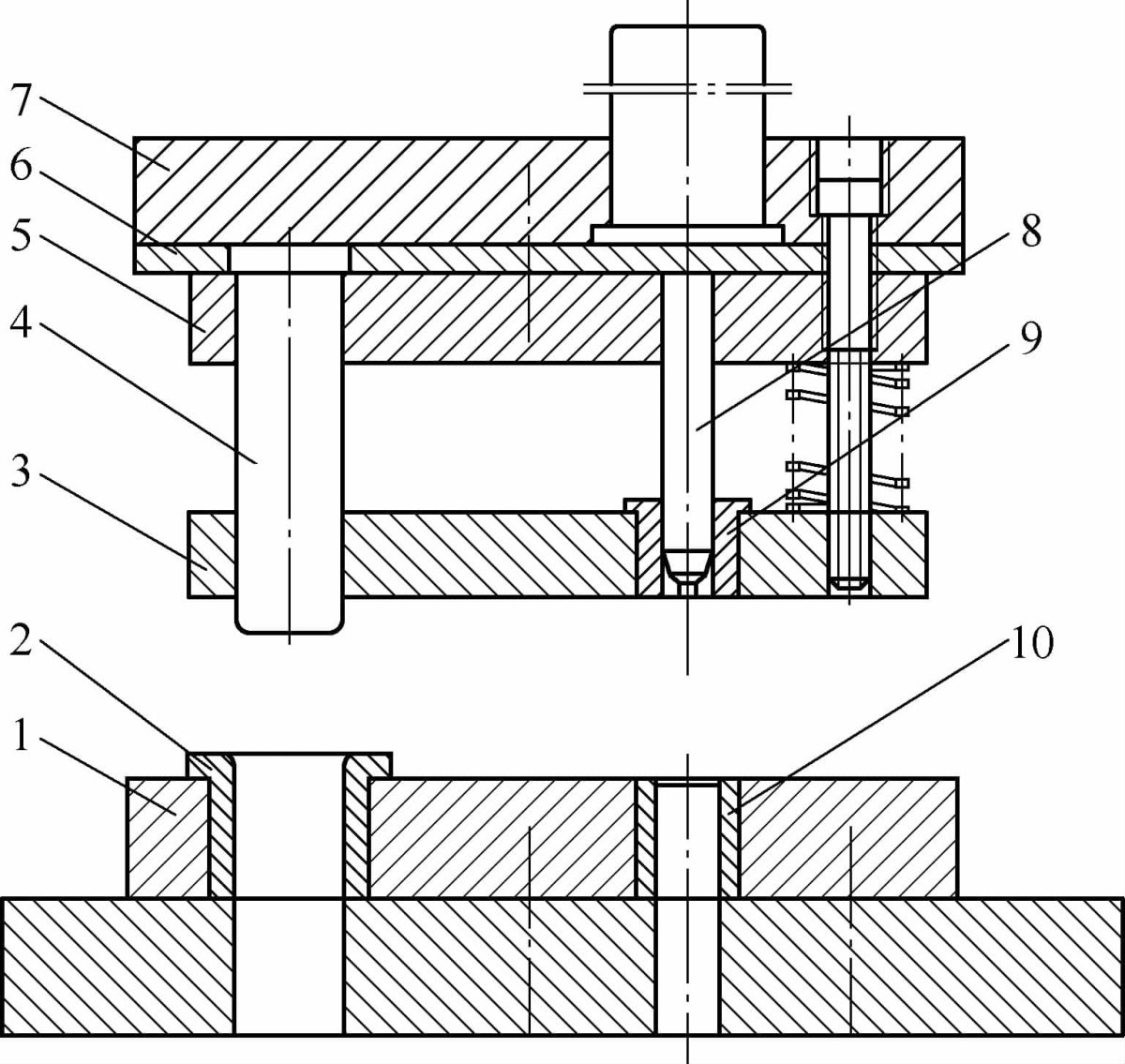
1—Matriz 2—Bucha guia 3—Placa de remoção 4—Poste guia 5—Placa retentora do punção 6—Placa espaçadora 7—Sapata superior da matriz 8—Punção 9—Luva guia 10—Inserção da matriz com liga dura
Para matrizes de flange de furo único de grande diâmetro com furos pré-fabricados, não são necessários postes-guia e buchas. A centralização é obtida alinhando a seção guia do punção com o furo pré-fabricado, seguido do posicionamento de acordo com o formato externo da peça, conforme ilustrado na Figura 5-22.
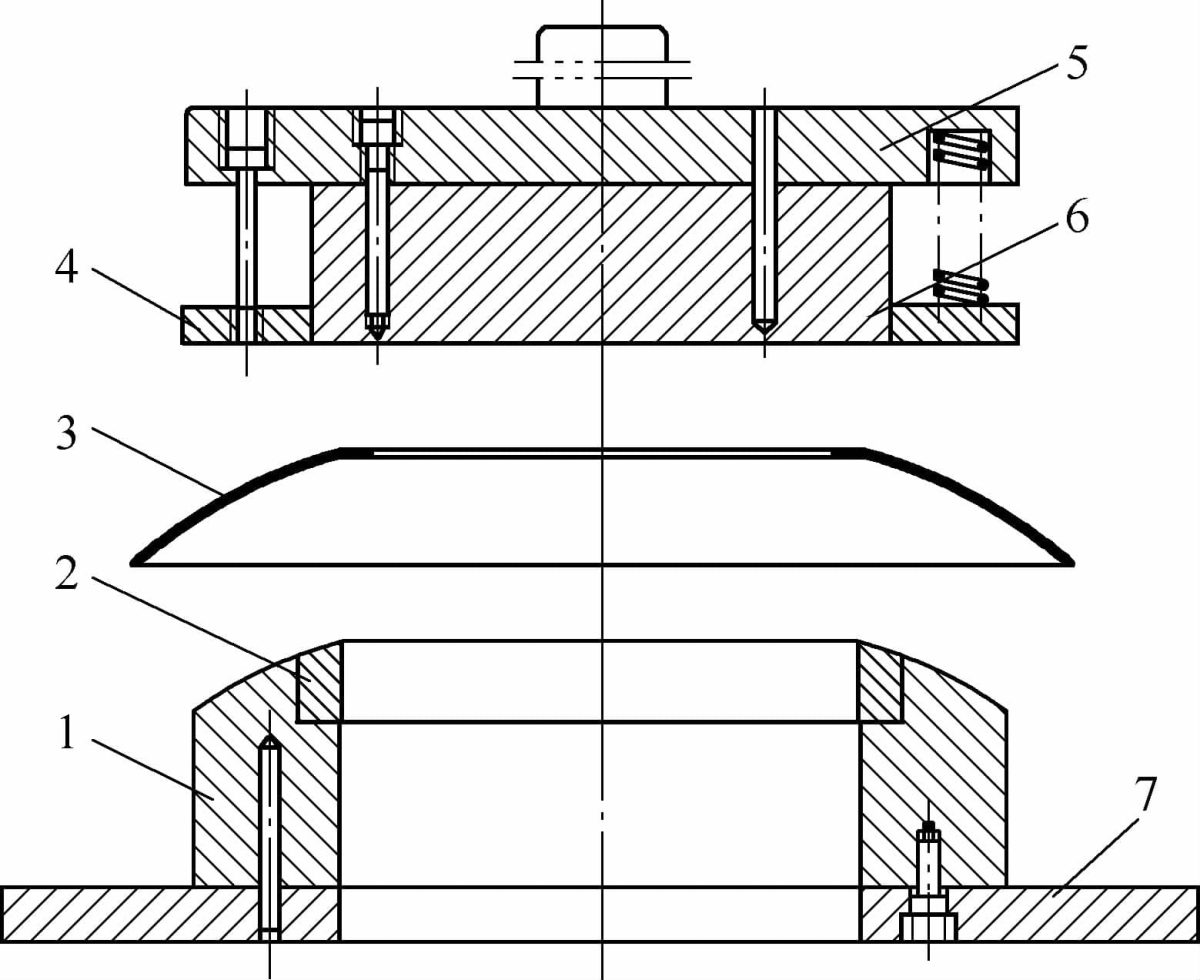
1—Inserção da matriz 2—Peça de trabalho 3—Revestimento da inserção da matriz 4—Anel ejetor 5—Sapata superior da matriz 6—Punção 7—Sapata inferior da matriz
As matrizes de flangeamento e rosqueamento geralmente devem ser equipadas com um mecanismo ejetor para desengatar a peça do punção. A peça de trabalho pode ser facilmente removida da matriz sob a ação da força de rebote, portanto, geralmente não há necessidade de considerar o uso de um removedor.
Porém, ao realizar machos de desbaste com deformação extensa ou quando a espessura do material for ≥4mm, o uso de um stripper deve ser considerado, conforme mostrado na Figura 5-23.

1—Punção 2—Anel de prensagem de borda 3—Matriz 4—Levantador.
Matriz de flangeamento de força assimétrica (alça plana de vaso de crisântemo)
Em teoria, peças flangeadas carregadas assimetricamente e peças dobradas assimetricamente podem ser processadas em peças simétricas para evitar que a peça se mova, completando ambas as peças ao mesmo tempo e, em seguida, cortando a peça ao meio após o flangeamento.
No entanto, uma vez que peças pequenas, como cabos de panelas, são frequentemente cortadas a partir do excesso de material nas bordas, o que não satisfaz as condições acima, esta descrição centra-se principalmente em matrizes de flange individuais.
Durante o processo de dobra única, o material é puxado pela força de flangeamento unilateral, resultando em deslizamento. A chave para projetar tais matrizes reside em evitar o deslizamento do material e garantir que a linha do flange esteja posicionada corretamente.
Antes do punção entrar em contato com a peça de trabalho, use uma placa de pressão móvel para fixar firmemente a peça de trabalho. A força de fixação deve exceder a força de flangeamento.
Incorporando vários fatores de compensação, a fórmula para estimar a força de flangeamento de materiais de aço inoxidável é a seguinte:
Na fórmula:
- F – força de flangeamento (N);
- L – comprimento da linha do flange (mm);
- t – espessura do material (mm);
- Rel. – limite de escoamento, que é fixado em 280 (MPa).
Atualmente, a maioria desses tipos de moldes utiliza predominantemente elastômeros de borracha como elemento elástico para aplicação de pressão. Os elastômeros de borracha oferecem benefícios significativos, como alta elasticidade, excelente desempenho de recuperação e resistência ao rasgo.
A espessura do elastômero de borracha não é necessariamente melhor quando aumentada; uma espessura ideal é geralmente três a quatro vezes a soma da altura do flange mais uma certa tolerância.
Se a pressão dentro da altura calculada for insuficiente, folhas de borracha mais finas podem ser colocadas em camadas, com finos calços de aço intercalados. Aumentar a área superficial da borracha pode aumentar a pressão aplicada. Para peças perfuradas com furos, é melhor usar o posicionamento dos furos conforme mostrado na Figura 5-24.
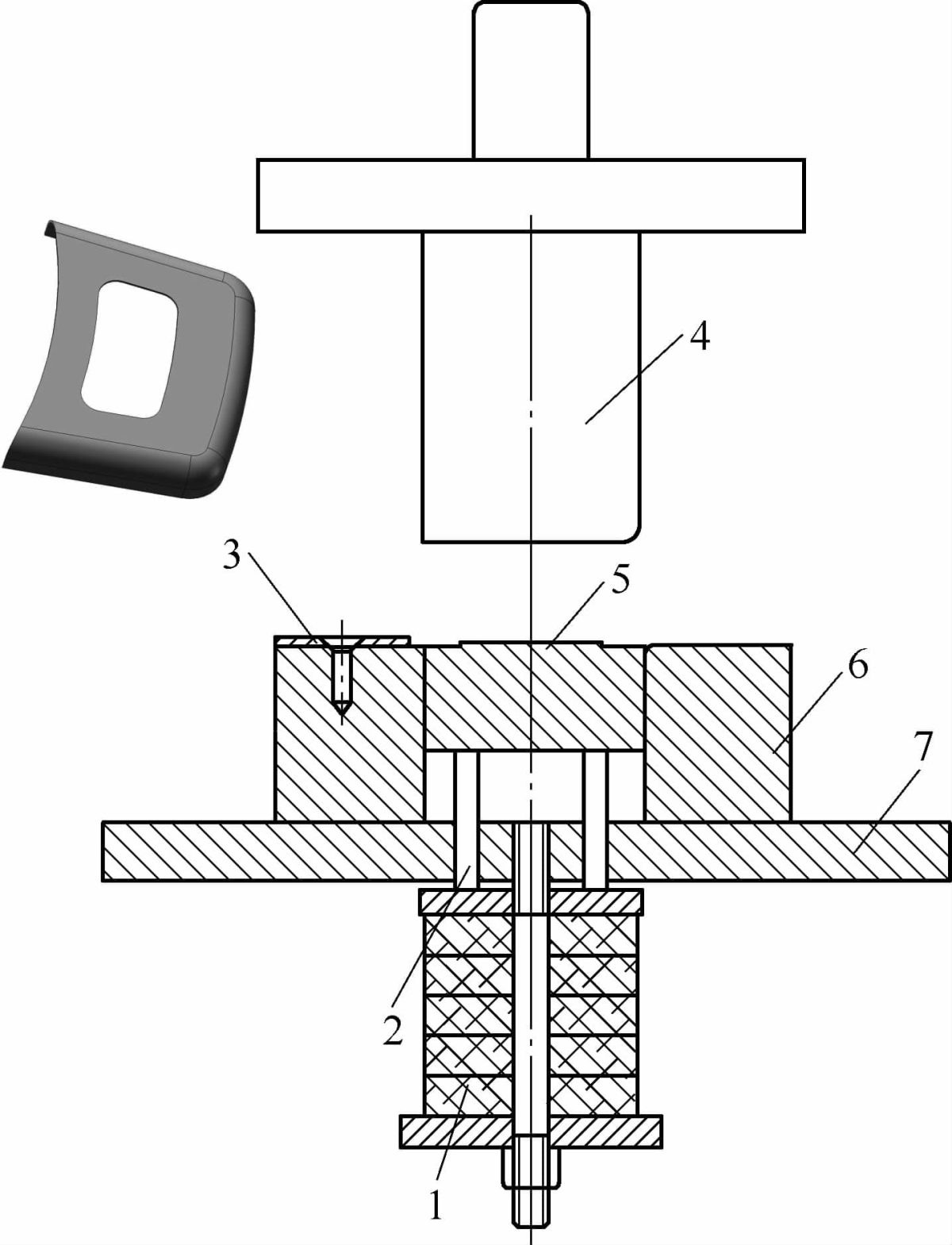
1) Elastômero de borracha, 2) Pino de transmissão de força, 3) Placa de localização, 4) Punção, 5) Placa cega, 6) Matriz e 7) Suporte inferior da matriz.
O bico do pote em formato de caqui apresenta borda enrolada
Durante o processo de brasagem entre o bico e o corpo de uma panela em forma de caqui, para conservar o caro material de brasagem de prata, é necessário formar uma flange vertical ao longo da linha de contorno da extremidade maior do corpo da panela. A operação de flangeamento na bica é realizada em uma prensa de bancada tipo cantilever, com a matriz colocada em posição invertida, conforme mostrado na Figura 5-25.
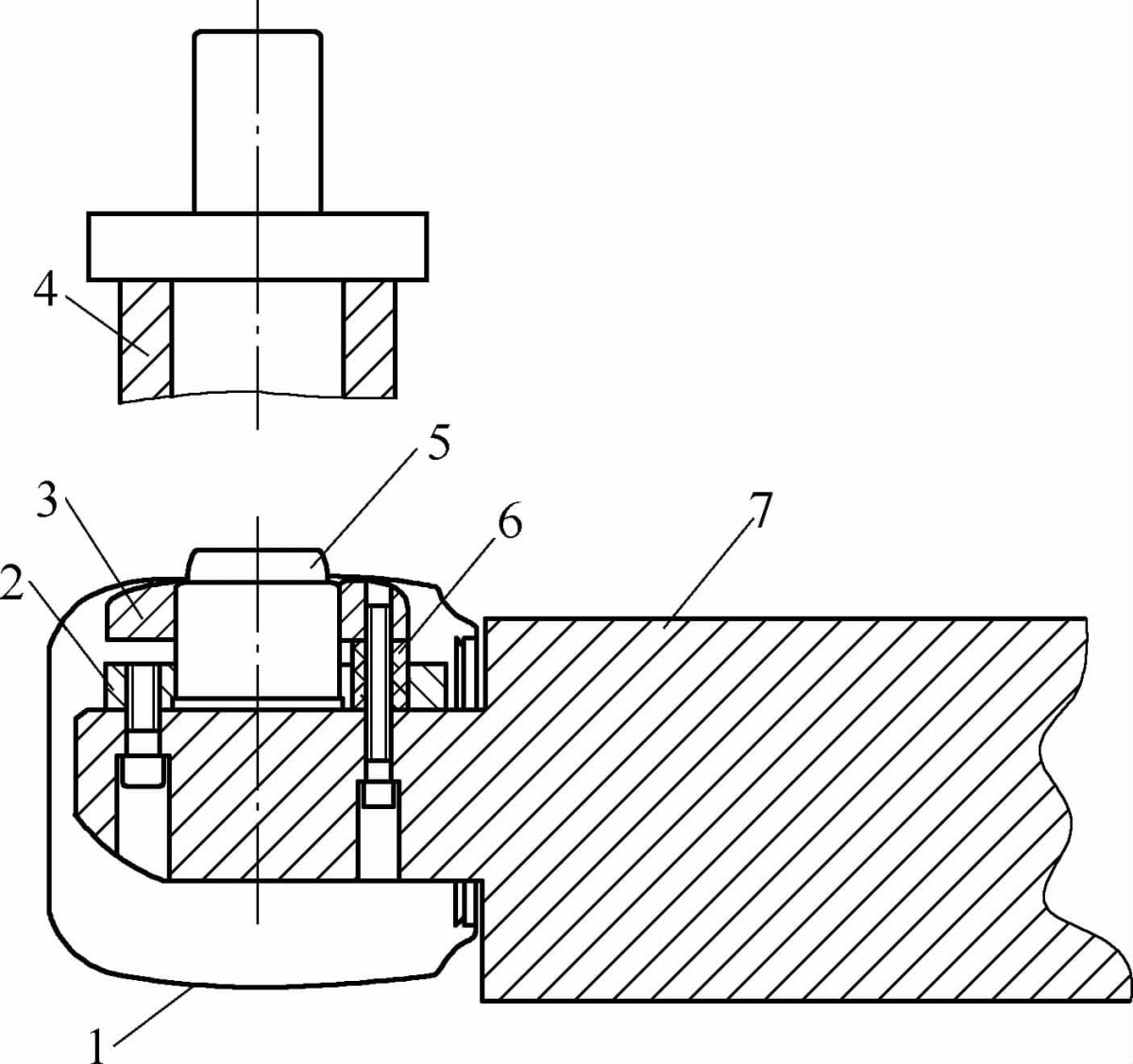
1. Corpo da chaleira, 2. Placa retentora do punção, 3. Suporte de placa, 4. Matriz, 5. Punção, 6. Elemento elástico, 7. Bancada de trabalho em balanço.
Durante a operação, coloque o corpo da chaleira pré-perfurado 1 na matriz de punção 5 com recursos de posicionamento. À medida que a matriz 4 desce, ela vence a resistência do elemento de mola 6 para flangear a peça de trabalho. Quando a matriz superior sobe, a placa de elevação 3 é levantada pela força da mola, liberando a peça da posição de flangeamento.
Na fase de projeto, é fundamental garantir que a distância vertical entre a bica da chaleira e a bancada em balanço exceda o curso do flange para evitar danos à bica.
Flangear em vez de enrolar (bico flangeado de uma chaleira)
Na produção de chaleiras de aço inoxidável, o bico é comumente processado usando uma técnica de flange duplo, conforme mostrado na Figura 5-26. Durante o projeto, a altura do primeiro flange deve ser moderada, variando de 4 a 6 vezes a espessura do material. A altura do segundo flange não deve ser muito pequena e deve variar de 8 a 12 vezes a espessura do material.
Nesta fase, a folga em ambos os lados do punção e da matriz deve ser aumentada para 1,5 a 2 vezes a espessura do material. Durante o segundo processo de flangeamento, a borda formada pelo primeiro flange será automaticamente pressionada firmemente contra o segundo flange, criando um efeito semelhante a uma borda ondulada.
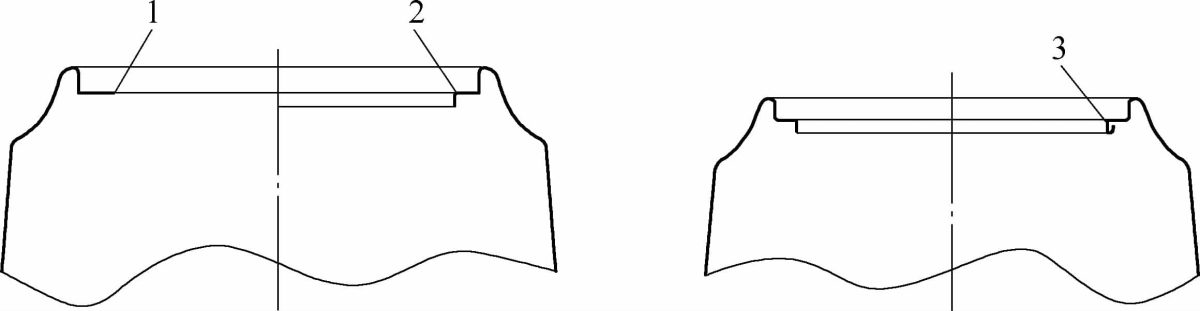
1. O efeito após perfurar o corpo da chaleira. 2. O primeiro flangeamento. 3. O segundo flangeamento.
Flangeamento de borda de matriz dura
A Figura 5-27 ilustra uma peça flangeada com arco arredondado, com espessura de material de 1,0mm e altura de flange de 12mm. Com base na experiência, para evitar enrugamento sob compressão, a altura do flange H não deve exceder 14 vezes a espessura (H≤14t). A matriz de formação é mostrada na Figura 5-28.
Normalmente, para aumentar a confiabilidade operacional, o arco do punção deve ser ligeiramente mais longo que o da peça de trabalho, com a matriz inferior sendo 6 a 10 mm mais larga que a matriz superior.
A inserção da matriz (3) pode ser feita de aço com baixo teor de carbono. A superfície de trabalho da placa de desgaste (9) é arredondada para servir principalmente à função do raio do canto da matriz (R). Processá-lo como um componente separado pode reduzir o consumo de aço para matriz ou aço para ferramentas de alta velocidade, diminuir a dificuldade de fabricação e permitir o ajuste fino da folga entre o punção e a matriz.
A placa perfuradora e decapante corresponde ao desenho do produto. A borda de trabalho da placa de desgaste é paralela à sapata da matriz. O material é gradualmente formado durante o curso descendente e finalmente ejetado da cavidade pela placa de remoção.
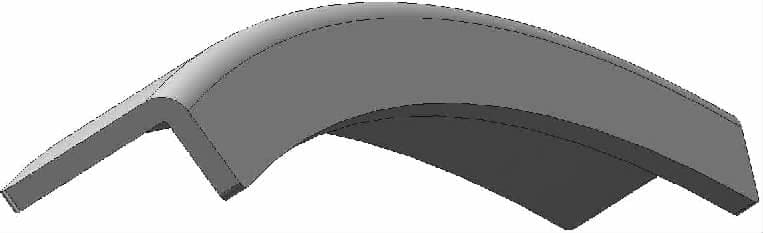
Alargamento de tubo com método de punção e bola em balanço
O tubo pode ser alargado para fora usando um punção em balanço com uma esfera de aço. O esquema da estrutura do molde é mostrado na Figura 5-29, que é adequado para flangeamento após um furo pré-fabricado ter sido processado no material do tubo.
O processo de trabalho do molde é o seguinte:
Primeiro, coloque uma esfera de aço com o diâmetro apropriado dentro do tubo no local de punção (perfuração), depois coloque o tubo na horizontal, encaixe o punção sobre ele e pressione a esfera de aço. Neste ponto, ligue a prensa e, à medida que a matriz superior se move para baixo, ela força o punção a se mover para baixo, empurrando a esfera de aço através do tubo.
Após o retorno da matriz superior, o punção levanta-se automaticamente, é removido do tubo e, assim, todo o processo de flangeamento é concluído.
A estrutura deste molde é simples e praticamente irrestrita na direção do comprimento, mas a resistência do cantilever do molde é limitada pelo diâmetro interno do tubo de aço. O flangeamento pode ser realizado em tubos mais grossos com diâmetro interno de 40 mm ou maior.
Neste projeto, um elastômero de borracha é adicionado abaixo da matriz superior para reduzir o ruído; e o parafuso limite pode ser ajustado para definir a altura do punção.
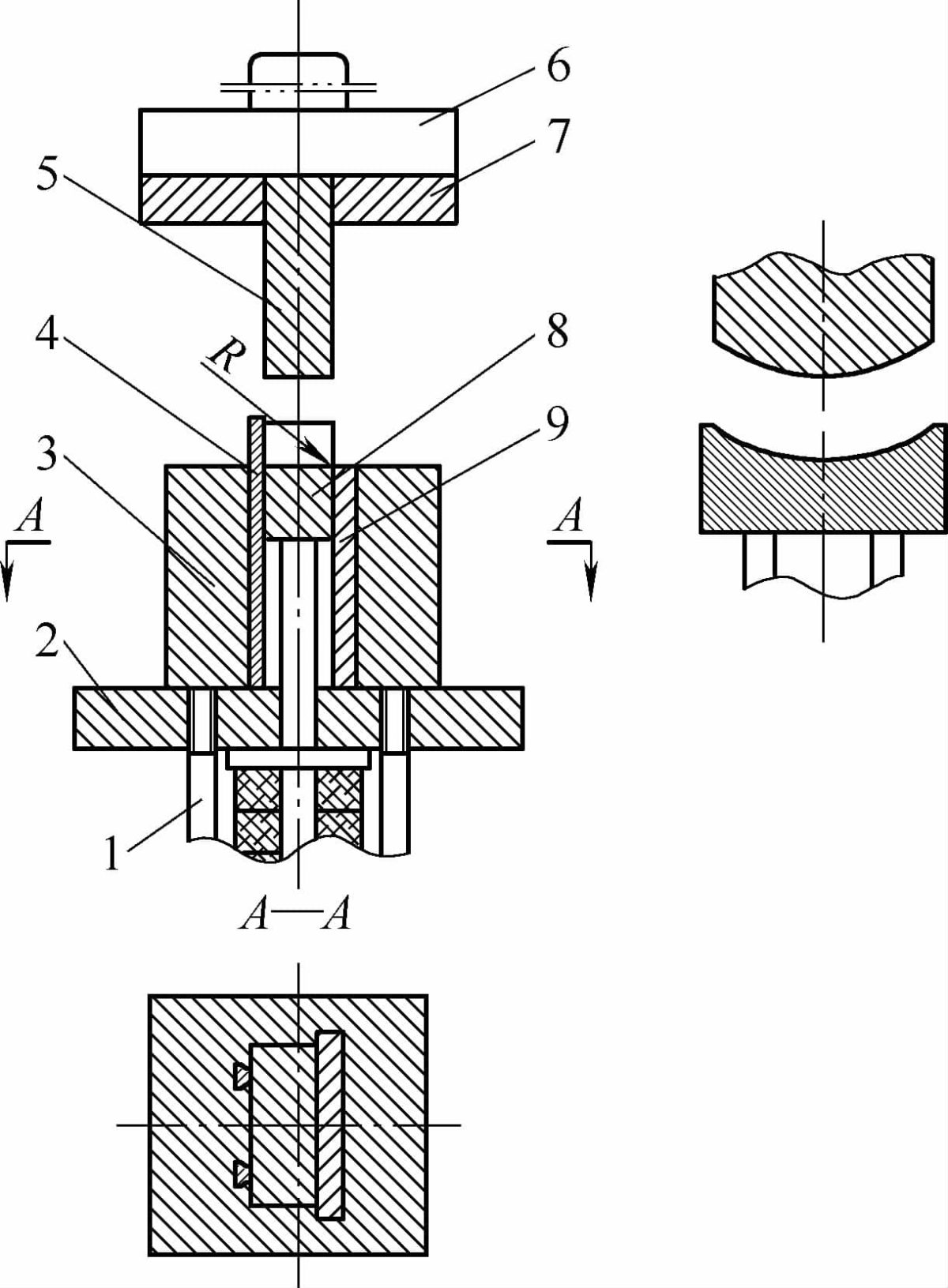
1. Mecanismo ejetor 2. Base inferior da matriz 3. Inserção da matriz 4. Localizador 5. Perfurador 6. Base superior da matriz 7. Placa retentora do perfurador 8. Placa de remoção 9. Placa rígida
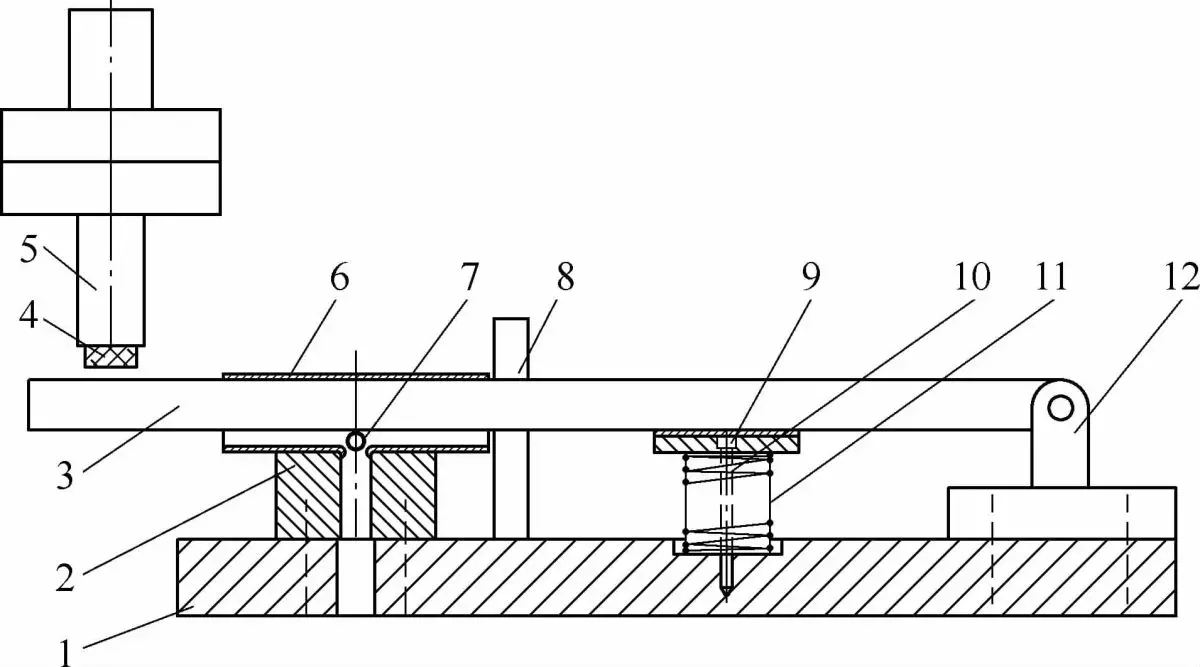
1. Suporte da matriz, 2. Matriz côncava, 3. Haste de pressão, 4. Elastômero de borracha, 5. Matriz superior, 6. Material do tubo, 7. Esfera de aço, 8. Parada de posicionamento do material do tubo, 9. Assento de elevação da haste de pressão, 10 . Parafuso Limite, 11. Mola, 12. Suporte.
Mandril de troca rápida para conversão de diâmetros internos em diâmetros externos, apresentando um anel de revestimento de malha metálica
A Figura 5-30 ilustra uma matriz formadora de boca de rede skimmer, que também pode ser usada para fabricar anéis de envolvimento para folhas de malha metálica de outros componentes cilíndricos, como filtros de ar de motor.
As partes principais da matriz consistem em um cone de expansão (8), blocos de expansão (4), molas de retorno (3 e 6) e uma base inferior da matriz (1).
Os blocos de expansão são dimensionados de acordo com o diâmetro interno da peça após a conformação. Eles são feitos de material que foi tratado termicamente e depois usinado.
Esses blocos são divididos em seções iguais e são cortados vãos específicos para garantir que, uma vez contraídos, mantenham uma folga razoável com o anel pré-fabricado. As molas de retorno (3 e 6) apertam os blocos de expansão (4) quando estão livres.
Quando o anel pré-fabricado (5) é encaixado sobre o bloco de expansão (4), a matriz fica na posição de reset e o diâmetro externo do bloco de expansão (4) é menor que o diâmetro interno do anel pré-fabricado (5).
À medida que a matriz superior se move para baixo, o bloco de pressão (7), impulsionado pela forte mola (10), supera a força ascendente da mola (2), forçando o bloco de expansão (4) a se mover para baixo e expandir para fora, aumentando sua força externa. diâmetro até que ele se encaixe perfeitamente no diâmetro interno da peça de trabalho. Quando o bloco de expansão desce totalmente, o seu diâmetro externo deixa de aumentar.
A matriz superior continua a descer, empurrando o anel pré-fabricado (5) para dentro da ranhura em R para formá-lo gradualmente. O material comprimido flui para cima ao longo do diâmetro externo da matriz superior, formando um novo diâmetro externo e criando uma folga designada com o diâmetro original para acomodar a folha de malha metálica.
À medida que a matriz superior sobe, a peça permanece na matriz inferior, e o bloco de expansão, sob a ação combinada da mola (2) e das molas de retorno (3 e 6), contrai-se em diâmetro, facilitando a remoção da peça.
Adicionando ou removendo calços (não mostrados no diagrama) abaixo da placa de suporte (12) ou do cone de expansão (8), o diâmetro dos blocos de expansão pode ser ajustado.
Esta matriz opera de forma confiável e não requer peças brutas de alta qualidade; pode até ser usado com anéis de material soldado.
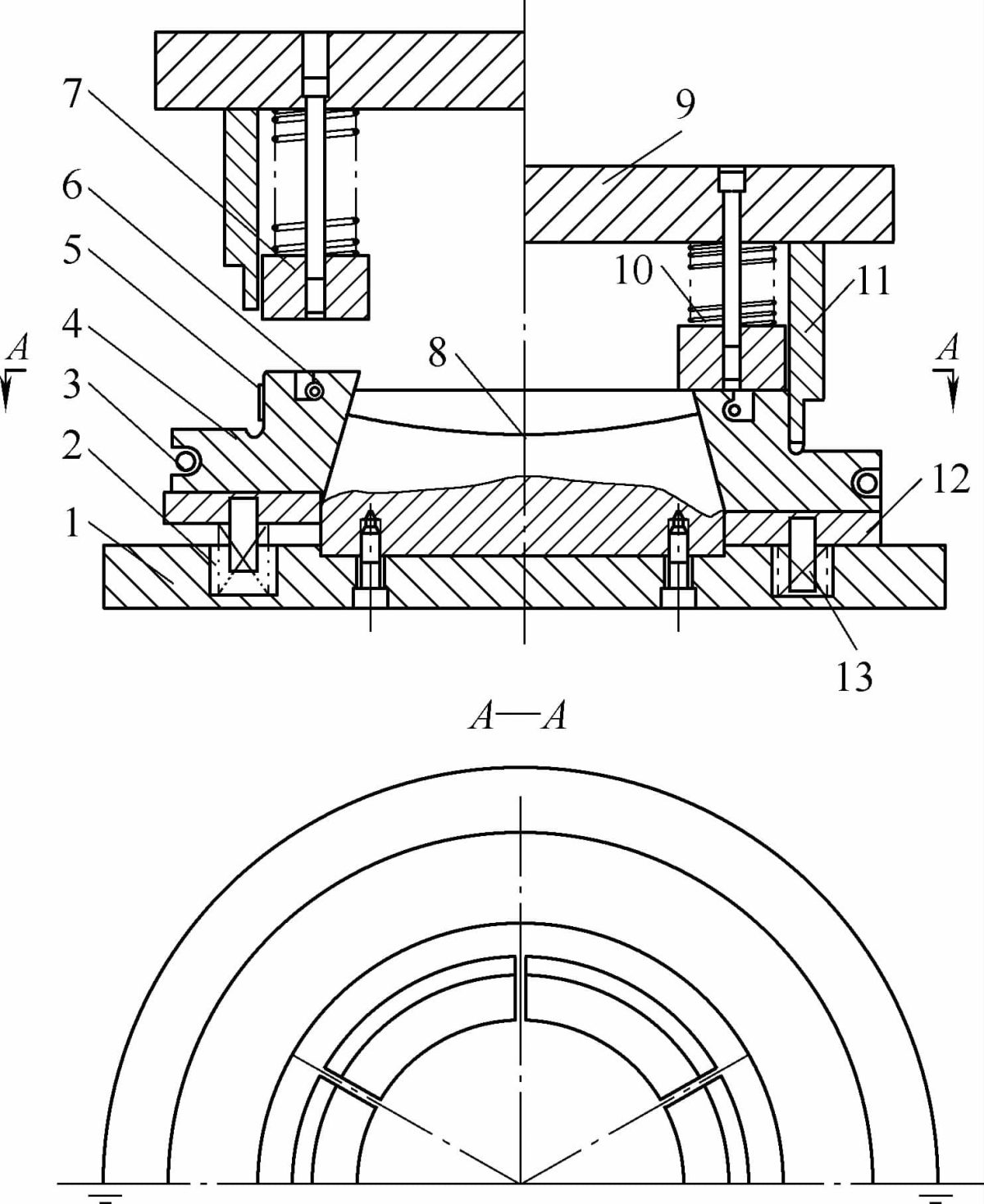
1 base, 2 molas, 3 e 6 molas de retorno, 4 blocos de expansão, 5 anéis pré-formados, 7 blocos de fixação, 8 mandris de expansão, 9 bases de molde superiores, 10 molas para serviço pesado, 11 moldes superiores, 12 placas de suporte, 13 centros de molas Alfinete
Matriz de flange superior e inferior
A Figura 5-31 ilustra uma matriz de flangeamento superior e inferior adequada para flangeamento de materiais espessos.
Formação de flange de extremidade de tubo
A conformação de flange de extremidade de tubo é um processo de conformação especializado que evoluiu das técnicas tradicionais de flangeamento por estampagem. Envolve a aplicação de pressão axial ao tubo através de uma matriz para induzir deformação por flexão localizada na borda da boca do tubo.
Essa técnica permite a fabricação de peças com as vantagens da simplicidade, menos etapas de processamento, menor custo e alta qualidade, podendo até produzir peças difíceis de conseguir com outros métodos de estampagem. Este processo tem sido amplamente adotado em setores industriais como automotivo e aeroespacial.
Existem dois métodos básicos de formação de flanges de extremidades de tubos: flangeamento externo e flangeamento interno, conforme mostrado na Figura 5-32.
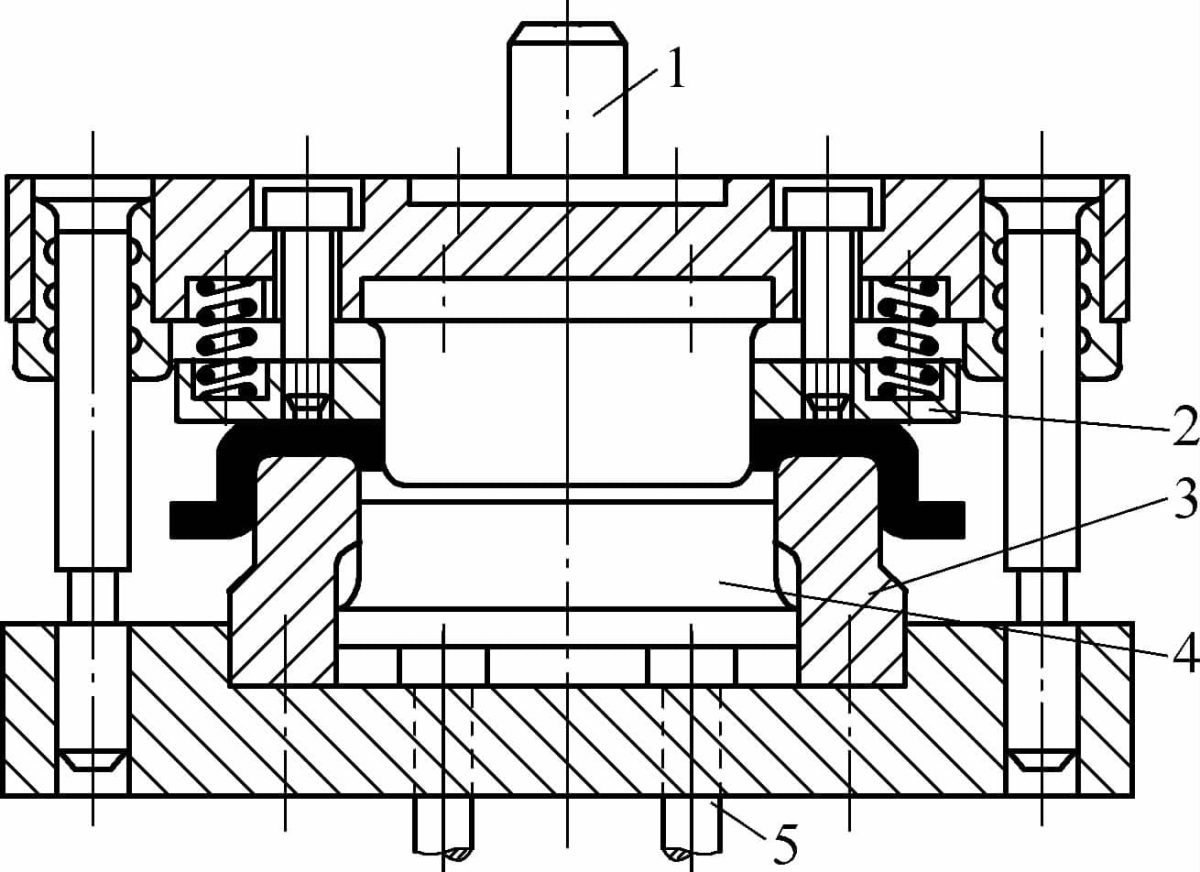
1 – Punção, 2 – Placa decapante, 3 – Matriz, 4 – Levantador, 5 – Ejetor de mola.
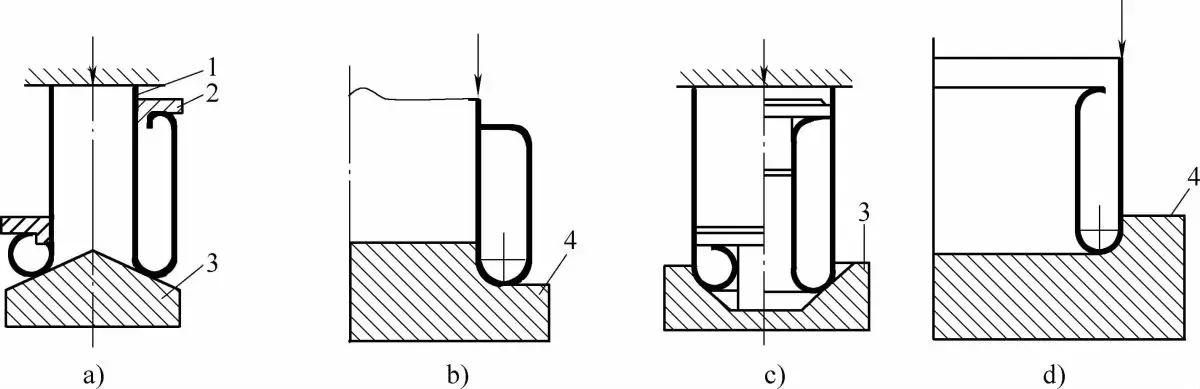
a) eb) Flange Externo; c) e d) Flange Interno.
1. Molde do tubo 2. Anel guia 3. Matriz cônica 4. Matriz de filete.
O processo de laminação de tubos não apenas forma efetivamente uma variedade de tubos cilíndricos de parede dupla e componentes de tubos multicamadas, mas também processa copos de fundo convexo, tubos escalonados, tubos de formato especial, bem como tubos duplos de meia parede, tubos anulares duplos. cilindros de parede, porcas ocas de parede dupla, trocadores de calor, silenciadores automotivos e guias de onda usados na indústria eletrônica.
Atualmente, esses componentes são geralmente fabricados usando métodos de estampagem e soldagem em múltiplas etapas, que são difíceis, caros e produzem superfície de baixa qualidade. O processo de laminação garante confiabilidade, leveza e economia de material para essas peças.
Uma ampla variedade de materiais tubulares é adequada para o processo de laminação, incluindo ligas de alumínio, aço de baixo carbono e aço inoxidável austenítico. Tubos com tamanhos variando de 5 mm x 0,5 mm a 250 mm x 5 mm podem ser enrolados com sucesso em tubos de camada dupla.

a) Tubo de laminação em forma de cone, b) Laminação de tubo + laminação, c) Laminação de tubo + alargamento, d) Tubo de laminação estirável.
A fiação do tubo é um processo de deformação complexo que envolve a transição da deformação por alargamento para a deformação por ondulação e, em seguida, para a deformação por rotação. Para garantir uma transição suave entre os modos de deformação, é essencial satisfazer as condições mecânicas, geométricas e de plasticidade durante a deformação. Os principais parâmetros do processo incluem a força de rotação, o ângulo do semicone da matriz, a espessura relativa da parede do tubo e as condições de plasticidade do material do tubo.
1) Giro Externo
Sob pressão axial, a peça bruta do tubo gira de dentro para fora, transformando a parede interna do tubo na parede externa. Este processo aumenta o diâmetro do tubo. Embora a carga de pressão externa engrosse ligeiramente a parede do tubo, a tensão de tração circunferencial produzida pela rotação externa é mais forte, levando a uma parede do tubo mais fina.
Os tipos de molde para fiação externa de tubos incluem principalmente matrizes cônicas, matrizes de ranhura anular e matrizes de fiação por estiramento. Ao processar tubos de camada dupla usando matrizes cônicas ou anulares, a parte superior do molde não apenas aplica pressão ao material do tubo, mas também precisa ser equipada com um anel guia para direcionar o material que já foi girado.
a) Matriz Cônica.
A matriz cônica é o tipo mais representativo de matriz giratória. Ao projetar uma matriz cônica, a principal consideração é determinar o ângulo do semicone (a) para satisfazer as condições de fiação. Com base nos cálculos tensão-deformação e plasticidade e considerando a influência do alongamento do material, o ângulo do semicone (a) deve atender à seguinte condição: 22,5° ≤ a ≤ 55°.
Semelhante ao alargamento do tubo, o diâmetro externo máximo do tubo fiado também é limitado pela taxa de alongamento do material. Em princípio, o tamanho do diâmetro de fiação pode ser escolhido livremente entre a taxa de alongamento do material e o raio mínimo de ondulação.
Quando uma grande diferença de diâmetro é necessária antes e depois da fiação, um ângulo de semicone maior deve ser usado. Por outro lado, um ângulo de semicone menor deve ser selecionado quando uma diferença de diâmetro menor for necessária.
As matrizes cônicas são versáteis, possuem baixo atrito, estruturas simples e são fáceis de fabricar. Entretanto, quando a peça bruta do tubo se deforma em uma matriz cônica, ela tende a deslizar, dificultando a centralização precisa.
A fiação está em estado de deformação livre, determinado apenas pelo princípio de resistência mínima e equilíbrio de tensões, e é significativamente afetada pela não uniformidade da estrutura do material, tornando difícil a produção de componentes tubulares de alta qualidade. Para evitar que a extremidade do tubo deslize na matriz cônica, um recurso de guia cilíndrica pode ser adicionado à cabeça do cone, resultando em uma melhoria notável, conforme mostrado na Figura 5-34a.
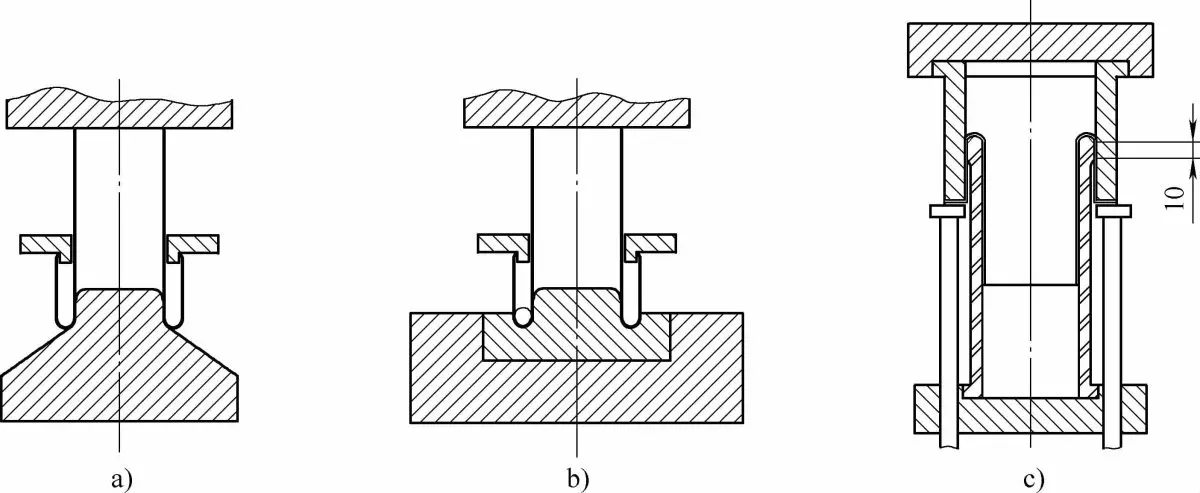
a) Matriz cônica de localização b) Matriz de raio ranhurado c) Matriz de alargamento extensível
(b) Molde de raio de ranhura anular.
A matriz de ranhura de canto radial é um tipo de matriz de alargamento de tubo derivada da matriz de flangeamento (flangeamento) da extremidade do tubo. Em uma matriz cônica com uma saliência de posicionamento, a interseção da saliência e da superfície cônica é feita em uma transição cônica para facilitar a ondulação e a deformação da peça bruta do tubo. Esta matriz apresenta excelentes propriedades de centralização.
À medida que o material do tubo é alargado, ele é restringido pelo raio r da ranhura circular, resultando em componentes de tubo consistentemente de alta qualidade, como mostrado na Figura 5-34b.
O projeto da matriz de ranhura de canto com raio envolve principalmente a determinação do raio r da ranhura circular. O tamanho de r não apenas determina o efeito de restrição na deformação da peça bruta do tubo no canto do raio, mas também determina a interferência geométrica entre o alargamento e a parte não deformada da peça bruta do tubo.
Portanto, é um parâmetro crítico do processo que deve ser maior ou igual ao raio de curvatura mínimo do material e menor ou igual ao raio permitido com base na taxa de alongamento do material.
Ao projetar a matriz de canto e ranhura com raio, não é necessário calcular o raio r. Em vez disso, pode ser fornecido com base na experiência e nas dimensões indicadas no desenho.
Para tubos de aço inoxidável, o raio de curvatura mínimo é normalmente
R=3t
onde t é a espessura do material.
O diâmetro máximo de alargamento do tubo para tubulação geral é
d=D(1+1,4A)
E para tubos soldados, o diâmetro máximo de alargamento do tubo é
d=D(1+1,3A)
onde:
- d – o diâmetro de alargamento do tubo (mm)
- D – o diâmetro da peça bruta do tubo (mm)
- A – taxa de alongamento do material (%)
(c) Matriz de flangeamento de estiramento.
Ao realizar o flangeamento de tubos com os tipos de molde mencionados acima, podem ocorrer defeitos como enrugamento induzido por instabilidade ou flexão da seção flangeada. Isso ocorre porque a peça bruta do tubo está sob tensão de compressão durante a deformação. Em contraste, o molde de flange estirável coloca a seção deformada da peça bruta do tubo sob tensão de tração quando submetida a carga externa, eliminando assim completamente o fenômeno de enrugamento durante o flangeamento.
Além disso, a zona de deformação é determinada pelo formato do molde, permitindo que a precisão dimensional da peça seja totalmente controlada pelo molde. Portanto, para componentes tubulares com requisitos rigorosos de precisão dimensional, um molde de flange extensível deve ser usado.
Para reduzir a resistência ao atrito na seção já flangeada, o comprimento útil do diâmetro externo do molde deve estar entre 8 e 12 mm, com as seções restantes escavadas conforme mostrado na Figura 5-34c.
Antes do molde do flange estirável começar a operar, a extremidade do tubo é primeiro expandida em uma face do flange para servir como superfície de fixação durante o estiramento. Conseqüentemente, o diâmetro externo do tubo formado pelo molde do flange estirável é sempre menor que o diâmetro externo máximo permitido pela taxa de alongamento do material.
(2) Flange Interno
Durante o flangeamento interno, o tubo bruto é enrolado de fora para dentro, resultando em um diâmetro externo menor após a conformação.
1) Flangeamento interno de matriz rígida.
O flange interno da matriz rígida raramente é usado nas práticas de produção. Isso ocorre porque o flangeamento interno é muito mais difícil em comparação com o flangeamento externo. O processo de formação do flangeamento interno é aquele em que o material engrossa continuamente.
Durante esse processo de espessamento, a estrutura cristalina do material deve ser reorganizada. A força necessária para o rearranjo da rede cristalina é mais de quatro vezes maior que a tensão de tração necessária para o alongamento do material (resistência à tração).
Como a resistência ao escoamento do material é sempre menor que a força necessária para o rearranjo da rede, o material do tubo torna-se instável e enruga-se antes mesmo de entrar no processo de flangeamento, impossibilitando a conclusão do flangeamento interno.
Na verdade, existem muitas técnicas alternativas ao flangeamento interno, incluindo o uso de tubos de menor diâmetro para flangeamento externo, bainha com rolo e redução do diâmetro por corte seguido de alongamento interno e flangeamento (veja a Figura 7-21).
Entre os métodos mencionados acima, o mais comumente usado é o flangeamento externo de tubos de pequeno diâmetro, que envolve o uso do tamanho do diâmetro interno do tubo vazio como o tamanho do diâmetro interno necessário do componente do tubo, enquanto o tamanho após o flangeamento externo torna-se o diâmetro do componente .
2) Flange interno do rolo.
Ao usar rolos para flangeamento interno, existem certas limitações entre a espessura e o diâmetro do material; especificamente, uma relação D/t ≥ 200 é necessária para que o processo prossiga sem problemas. Caso contrário, a resistência causada pela agregação do material pode ser excessiva, resultando num diâmetro externo poligonal da peça.
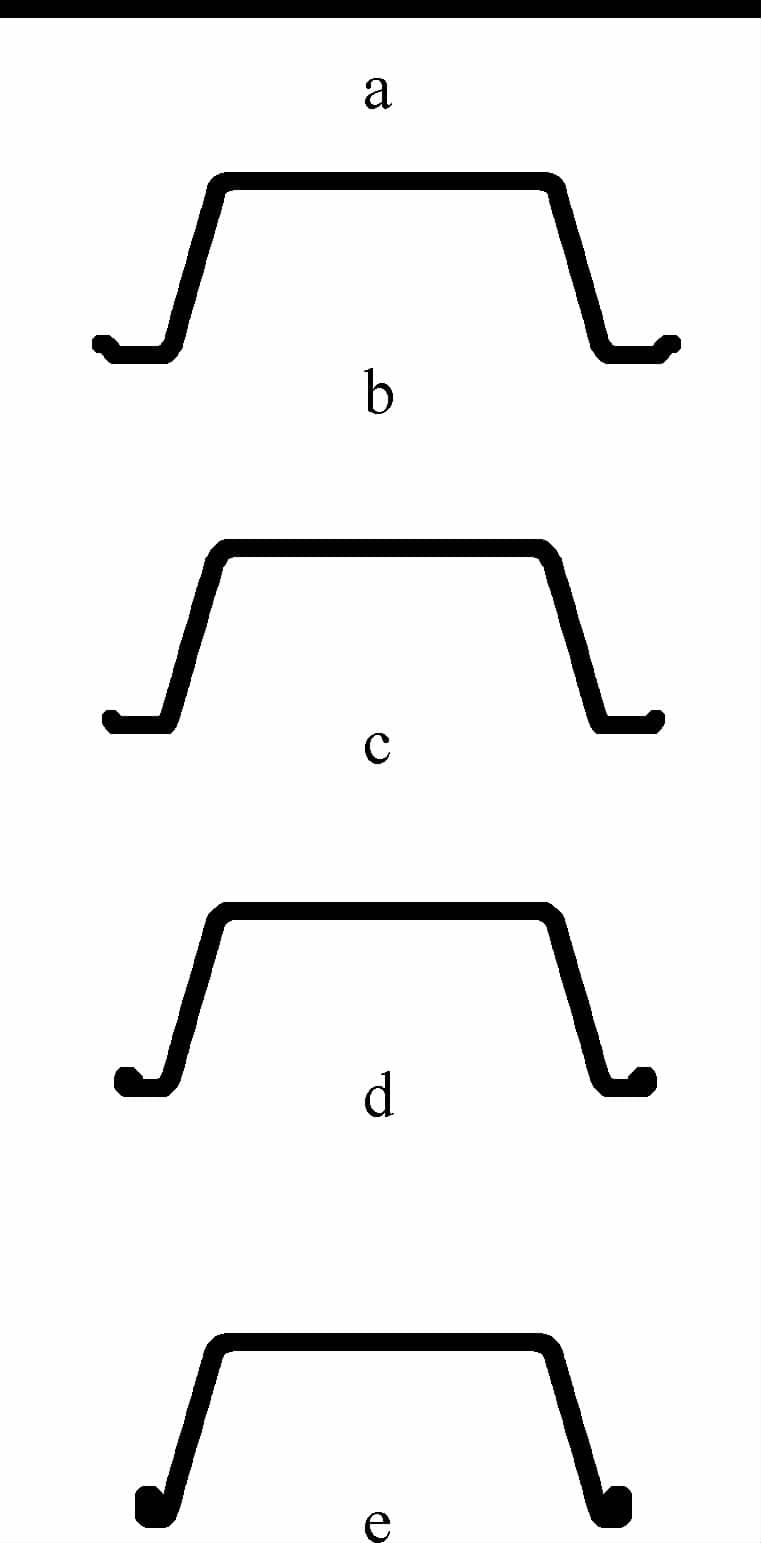
a) Corte da folha circular b) Desenho c) Recorte d) Flange e) Bainha
Processo de formação de tigela
Uma tigela é essencialmente uma versão ampliada de uma bacia projetada para aumentar a capacidade. Para aumentar sua resistência, um degrau de flange é adicionado à borda laminada, conforme ilustrado na Figura 5-35.
O processo de laminação é estrategicamente colocado antes do flangeamento para evitar enrugamento do flange. Embora o mecanismo de deformação da seção laminada durante o flangeamento ainda não seja totalmente compreendido, ele provou ser praticamente eficaz.