Os seguintes fatores desempenham um papel crítico no processo de corte a laser:
- Modo laser
- Potência laser
- Posição de foco
- Altura do bico
- Diâmetro do bico
- Gases auxiliares
- Pureza do gás auxiliar
- Fluxo de gás auxiliar
- Pressão de gás auxiliar
- Velocidade de corte
- Material em folha
- Qualidade da superfície da chapa (por exemplo, ferrugem, detritos, etc.)
Os parâmetros do processo associados ao corte a laser são mostrados na figura abaixo.
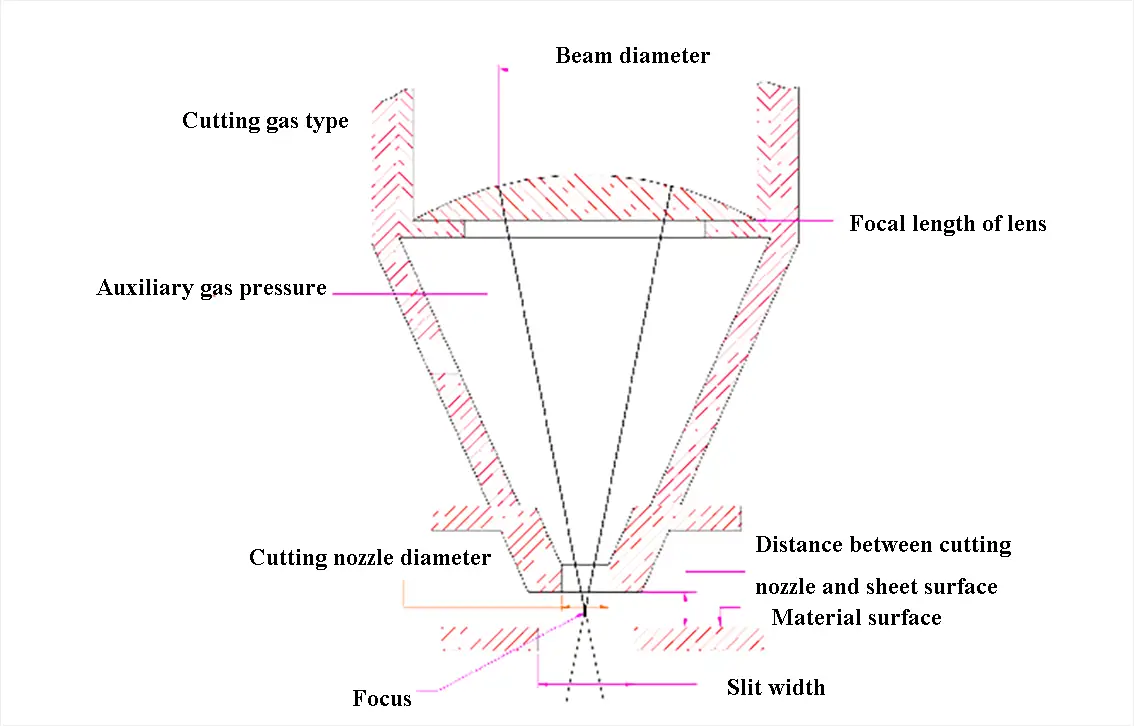
Fig. 1 Parâmetros do processo de corte
I. Modo Laser
O modo laser impacta muito o processo de corte e produz melhores resultados no corte de chapas de aço. Isto está intimamente ligado ao modo laser e à qualidade da lente óptica externa.
A distribuição da intensidade da luz através da seção transversal do feixe de laser é chamada de modo transversal do laser. O modo transversal é geralmente considerado o modo laser.
Vários modos transversais são representados pelo símbolo TEMmn, onde TEM significa onda eletromagnética transversal e M e N são inteiros positivos que representam os números ordinais de pontos com intensidade de luz zero nas direções do eixo X e do eixo Y, respectivamente, conhecidos como o modo ordinal.
A figura a seguir mostra os focos de vários modos transversais diferentes do feixe de laser. O modo TEM00, também conhecido como modo básico, não possui pontos com intensidade de luz zero. O modo TEM10 possui um ponto de intensidade zero na direção X e o modo TEM01 possui um ponto de intensidade zero na direção Y. Quanto maiores os ordinais de modo M e N, mais pontos com intensidade de luz zero no foco.
Os feixes de laser com vários modos transversais são chamados de multimodo.
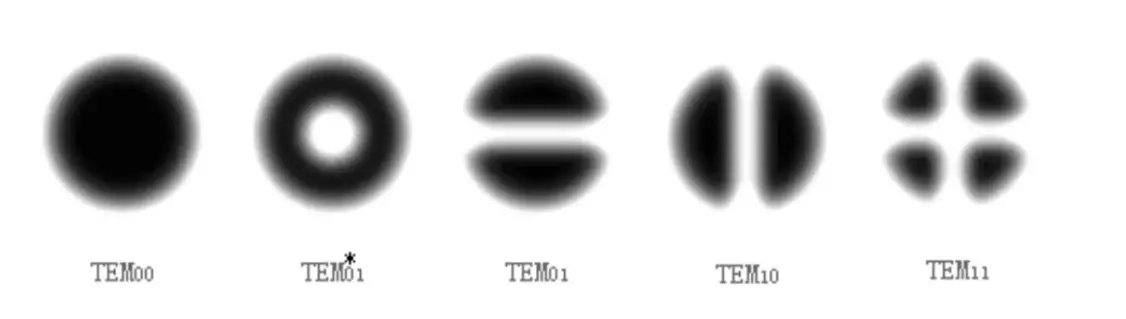
Fig. 2 Modo Spot
Na figura mencionada acima, o modo TEM00 é referido como modo fundamental.
O modo TEM*01 é um modo de toque único e também é conhecido como modo quase fundamental. Um asterisco * é adicionado para distingui-lo do TEM01.
Na realidade, o modo TEM01 e o modo TEM10 podem ser considerados o mesmo modo, pois os eixos X e Y são divididos artificialmente. Os estereogramas de vários modos são mostrados abaixo.
Figura 3: Estereograma do modo TEM00
Figura 4: Estereograma do modo TEM20
Figura 5: Estereograma do modo TEM23
Figura 6: Estereograma do Multimodo.
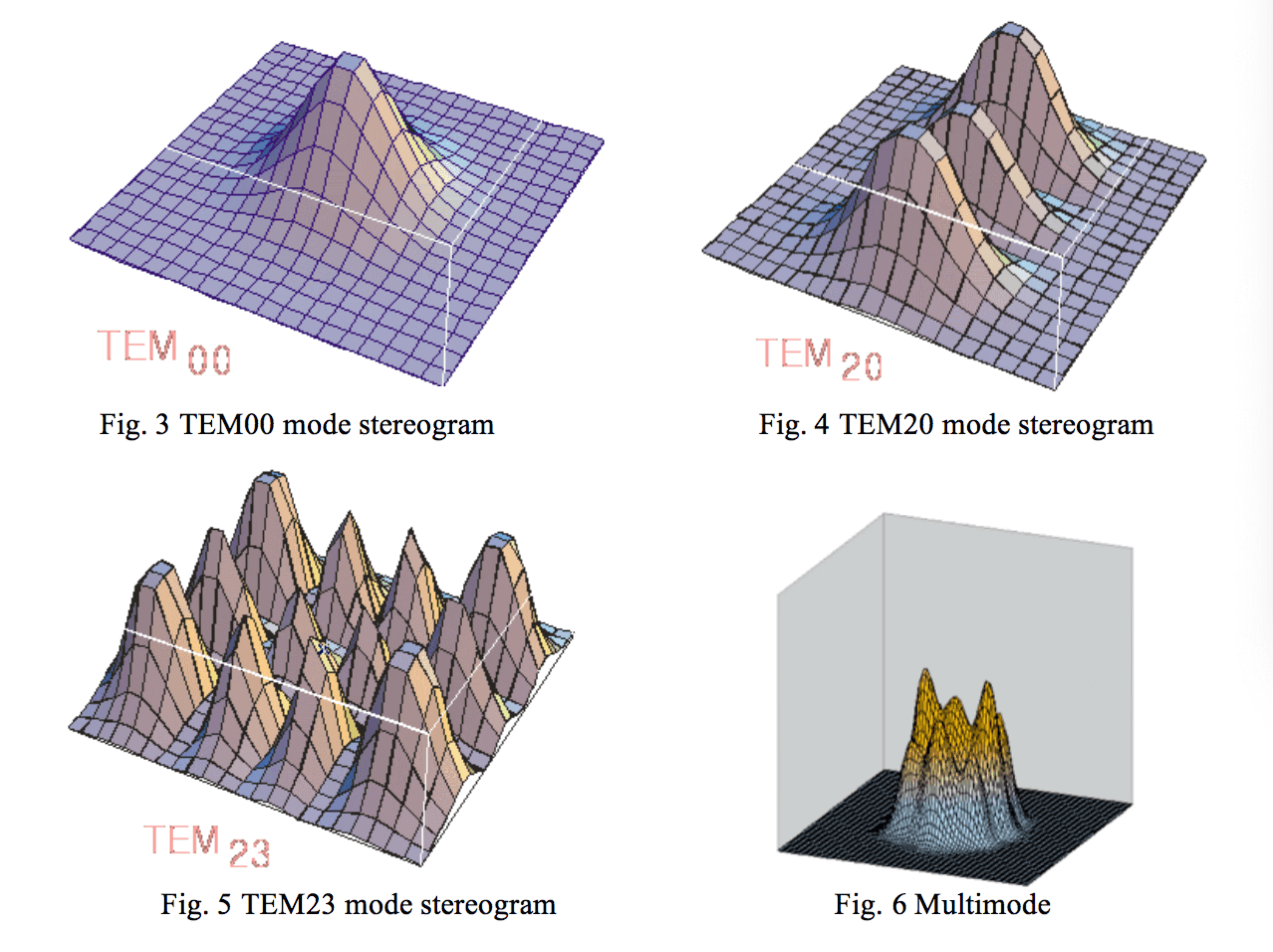
II. Posição focal
A posição do foco é um parâmetro crucial e deve ser adequadamente ajustada.
1. A relação entre a posição do foco e a superfície de corte
Posição focal | Diagrama esquemático | Características |
Distância focal zero:
O foco está na superfície da peça. |
![]() |
É adequado para aço carbono fino abaixo de 5 mm.
(seção cortada) ![]()
Quando o foco está na superfície superior da peça de trabalho, o resultado do corte é suave na superfície superior, mas a superfície inferior não é lisa. |
Distância focal negativa:
O foco está sob a superfície da peça de trabalho. |
![]() |
Alumínio, aço inoxidável e outras peças adotam este método.
(seção cortada) ![]() O foco está localizado no centro e na parte inferior, resultando em uma área maior de superfície lisa. Os resultados indicam que a largura de corte é maior e o fluxo de gás de corte é maior com foco neste local, em comparação com um foco com distância focal zero. Além disso, o tempo de perfuração é maior nesta posição de foco. |
Distância focal positiva:
O foco está na superfície da peça de trabalho |
![]() |
Ao cortar placas de aço espessas, é utilizado oxigênio. A oxidação do oxigênio utilizado no corte deve ocorrer de cima para baixo. Para acomodar a espessura da placa, é necessária uma largura de corte maior, o que pode ser conseguido ajustando as configurações. A seção de corte se assemelha à do corte a gás, com oxigênio soprando e produzindo uma seção áspera. |
2. A influência da posição do foco na seção de corte
1,5 mm acima da superfície | 0,5 mm acima da superfície | 2,5 mm acima da superfície |
![]() |
![]() |
![]() |
3. Busca de foco
O conceito básico é usar cola de máscara para bloquear o bico e ajustar a distância do foco. Em seguida, o tamanho dos furos é verificado. A posição com o menor furo é o foco. Finalmente, o melhor foco para corte é determinado com base no processo de corte após o foco ter sido encontrado.
III. Bocal
O formato do bico, o diâmetro do bico e a altura do bico (a distância entre a saída do bico e a superfície da peça de trabalho) afetarão o resultado do corte.
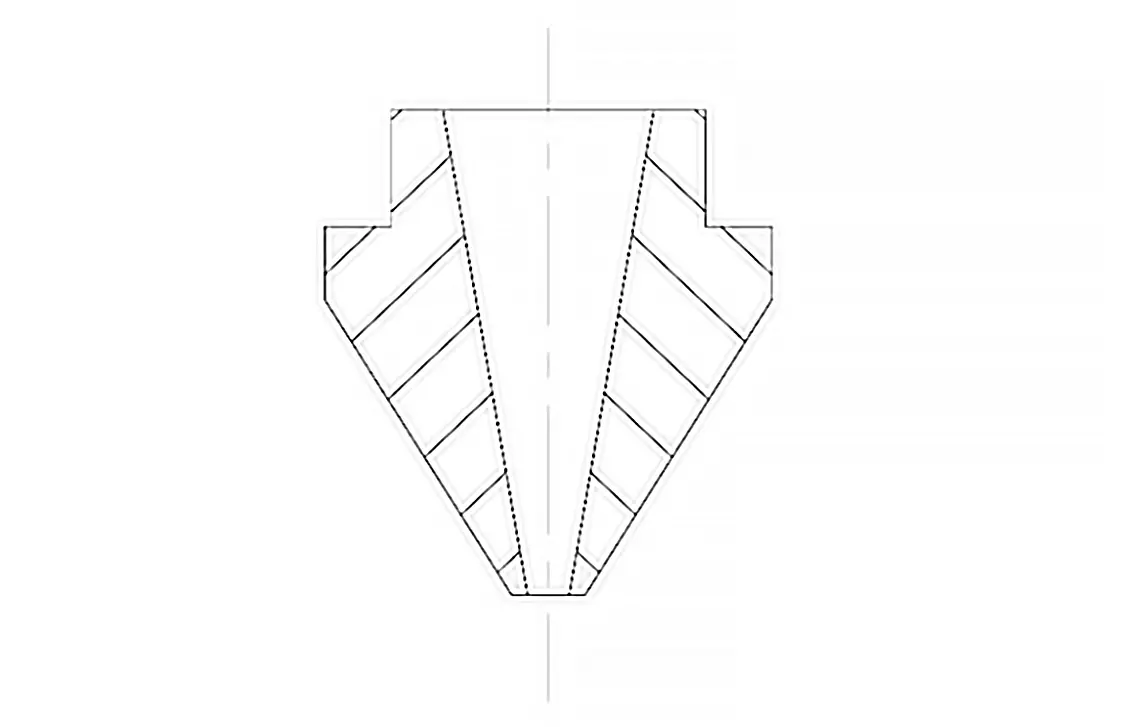
Fig. 7 Bocal
1. Função do bico
- Ajuda a evitar que impurezas, como resíduos de derretimento, saltem para cima, passem pelo bico e contaminem a lente de foco.
- Regula a área e o tamanho da difusão do gás para controlar a qualidade do corte.
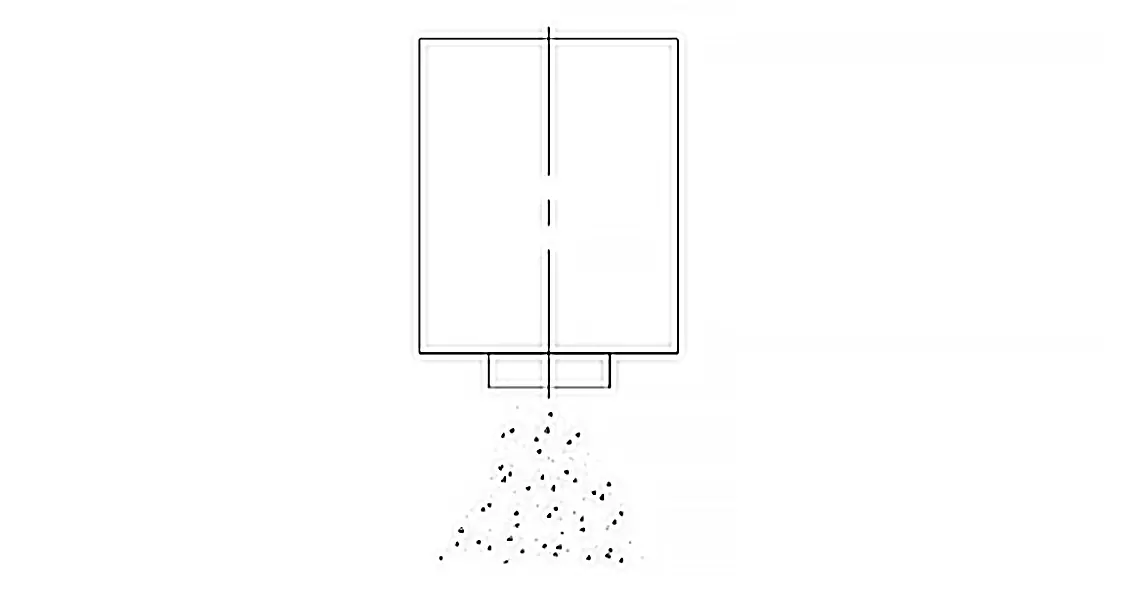
Fig. 8 Ejeção de gás sem bico
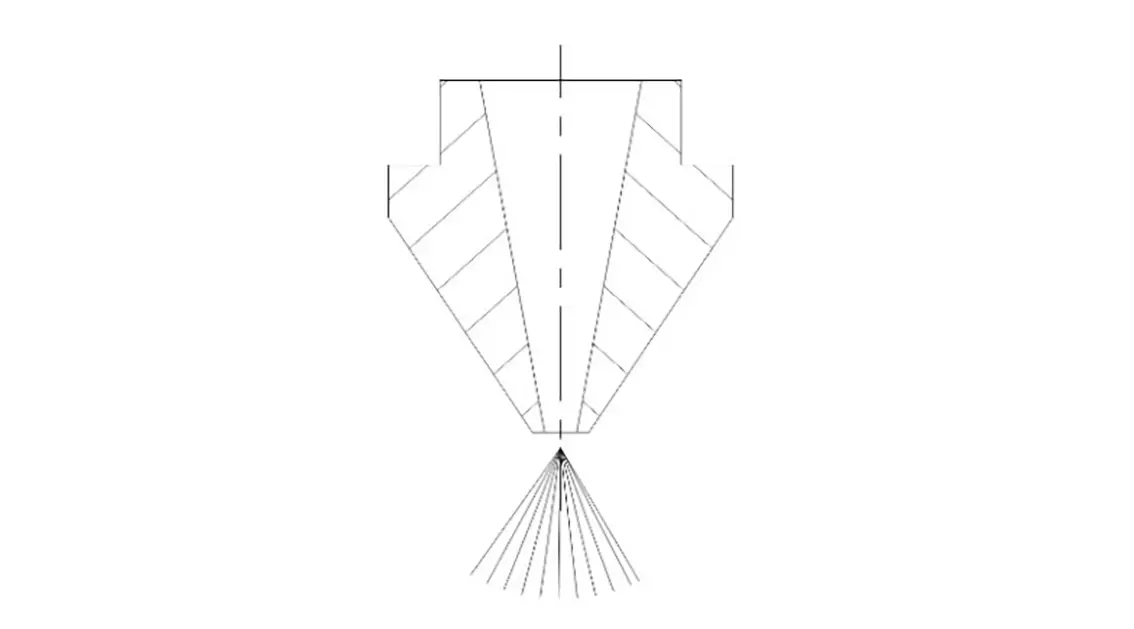
Fig. 9 Ejeção de gás com bocal
2. A relação entre bico e qualidade de corte
A coaxialidade entre o centro do orifício de saída do bico e o feixe de laser é um dos fatores importantes que afetam a qualidade do corte. Quanto mais espessa for a peça, maior será a influência. A coaxialidade será diretamente afetada quando o bico se deformar ou houver uma mancha derretida.
Portanto, o bico deve ser armazenado com cuidado para evitar danos e deformações. O formato e o tamanho do bico possuem alta precisão de fabricação e deve-se prestar atenção ao método correto de instalação.
Se a condição do bico for ruim, pode ser necessário alterar as condições de corte e é melhor substituí-lo por um novo. Se o bico não estiver alinhado com o eixo do laser, isso afetará a qualidade do corte da seguinte forma.
1) Influência na seção de corte
Conforme ilustrado na figura, quando o gás auxiliar é expelido do bocal, o volume do gás torna-se irregular, com manchas derretidas de um lado, mas não do outro. O volume irregular de gás tem pouco impacto no corte de chapas finas com menos de 3 mm, mas torna-se mais sério ao cortar chapas mais grossas, às vezes até impedindo um corte bem-sucedido.
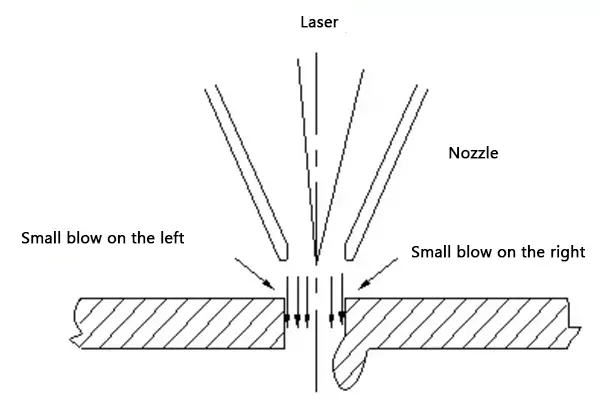
Fig. 10 Influência da coaxialidade na seção de corte
2) Impacto em cantos vivos
Se a peça de trabalho tiver ângulos agudos ou pequenos, ela estará sujeita ao derretimento excessivo, o que pode impedir o corte de placas grossas.
3) Impacto na perfuração
Podem ocorrer instabilidade de perfuração, dificuldades em controlar o tempo, fusão excessiva de placas espessas e dificuldade em dominar as condições de penetração. No entanto, esses problemas têm pouco efeito no corte de chapas finas.
3. Ajuste de coaxialidade entre o orifício do bico e o feixe de laser
As etapas para ajustar a coaxialidade entre o orifício do bico e o feixe de laser são as seguintes:
(1) Aplique tinta na face final de saída do bico (geralmente em vermelho) e prenda fita adesiva na face final de saída do bico, conforme mostrado na figura.
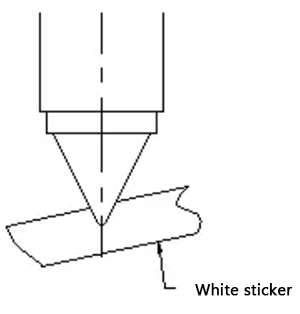
Fig. 11 Etapa 1 de ajuste coaxial
(2) Use uma potência de 10-20 watts para perfuração manual.
(3) Retire o papel autoadesivo, tomando cuidado para manter sua orientação para comparação com o bico.
Em condições normais, o laser queimará uma mancha preta no papel autoadesivo. Contudo, se o centro do bico se desviar muito do centro do feixe de laser, o ponto preto não será visível (pois o feixe de laser atingirá a parede do bico).
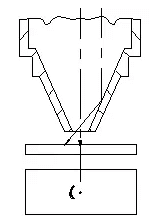
Fig. 12 Desvio do bico muito grande
(4) Se o ponto central for muito grande ou pequeno, verifique se as condições são consistentes e se a lente de foco está segura.
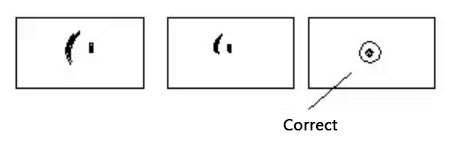
Fig. 13 Espelho de foco solto
(5) Observe a direção do ponto preto em relação ao centro do bico e ajuste a posição do bico de acordo.
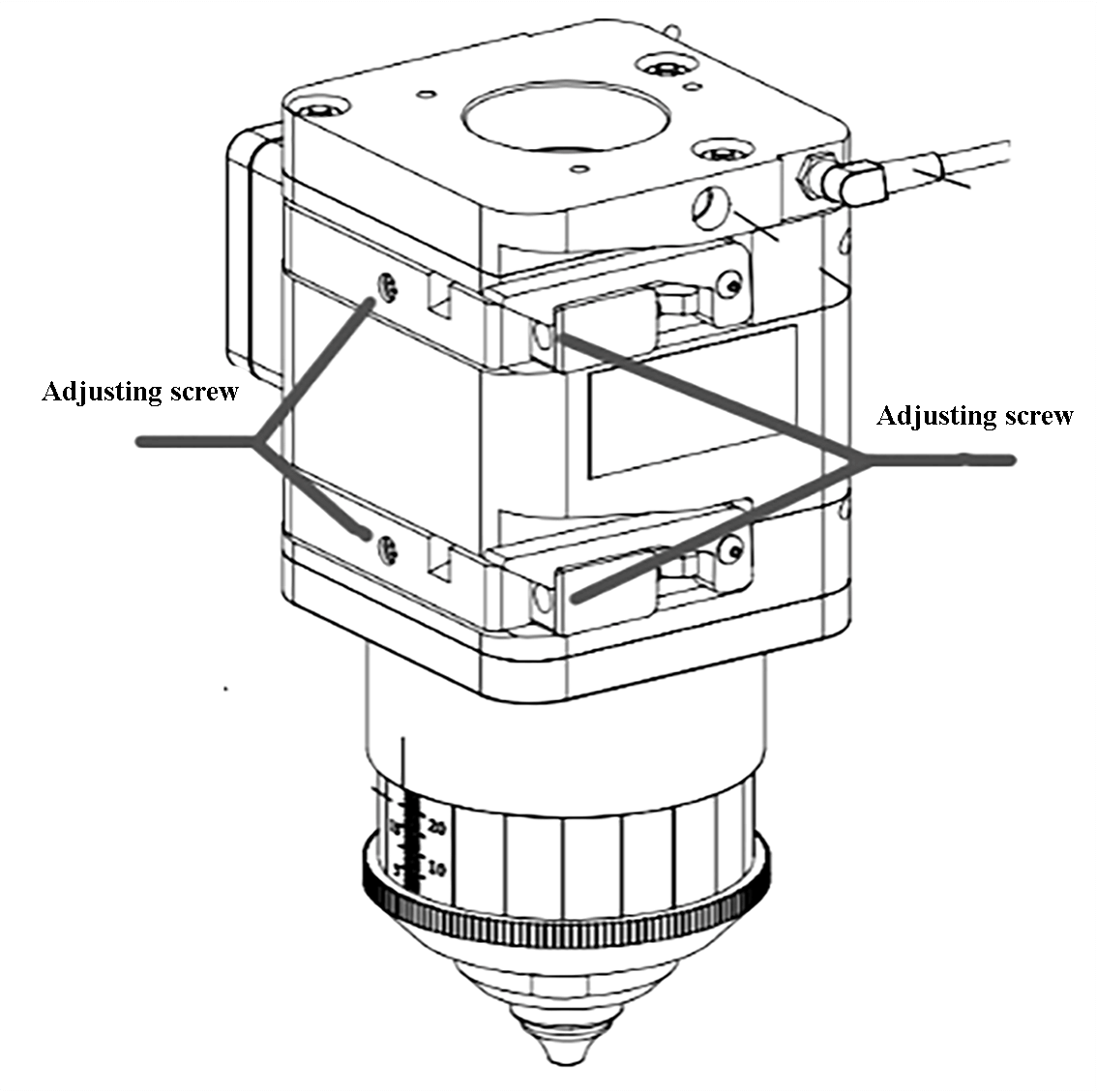
Fig. 14 Ajustando a posição do feixe de laser coaxial
4. Diâmetro do bico
O tamanho da abertura tem um impacto crucial na qualidade do corte e da perfuração. Se a abertura do bico for muito grande, o material derretido poderá espirrar durante o corte e passar pelo orifício do bico, podendo danificar a lente. Quanto maior a abertura, maior a probabilidade de isso ocorrer, levando à diminuição da proteção da lente de foco e à menor vida útil da lente.
Comparação da abertura do bico
Abertura do bico | Taxa de fluxo de gás | Capacidade de remoção de fusão |
Pequeno | Rápido | Grande |
Grande | Lento | Pequeno |
A diferença entre o bico φ1 e φ1,5
Diâmetro do bico | Placa fina (menos de 3 mm) | Placa espessa (mais de 3 mm)
Alto poder de corte, maior tempo de resfriamento e maior tempo de corte |
φ1 | A superfície de corte está boa. | A área de difusão do gás é pequena e instável, mas está basicamente disponível. |
φ1,5 | A superfície de corte será mais espessa e o canto é fácil de ter manchas de solução | A área de difusão do gás é grande, a velocidade do gás é lenta e o corte é estável. |
5. Ajuste da altura do bico
A altura do bico refere-se à distância entre a saída do bico e a superfície da peça. A faixa para definir esta altura está entre 0,5 mm e 4,0 mm, com uma configuração típica de 0,7 mm a 1,2 mm para corte.
Se a altura for definida muito baixa, o bico poderá colidir com a superfície da peça de trabalho. Por outro lado, se for definido muito alto, a pressão e a concentração do gás auxiliar diminuirão, levando a um declínio na qualidade do corte. Durante a perfuração, a altura deve ser um pouco maior, em torno de 3,5 mm-4 mm, para evitar que a lente de foco seja contaminada por respingos de perfuração.
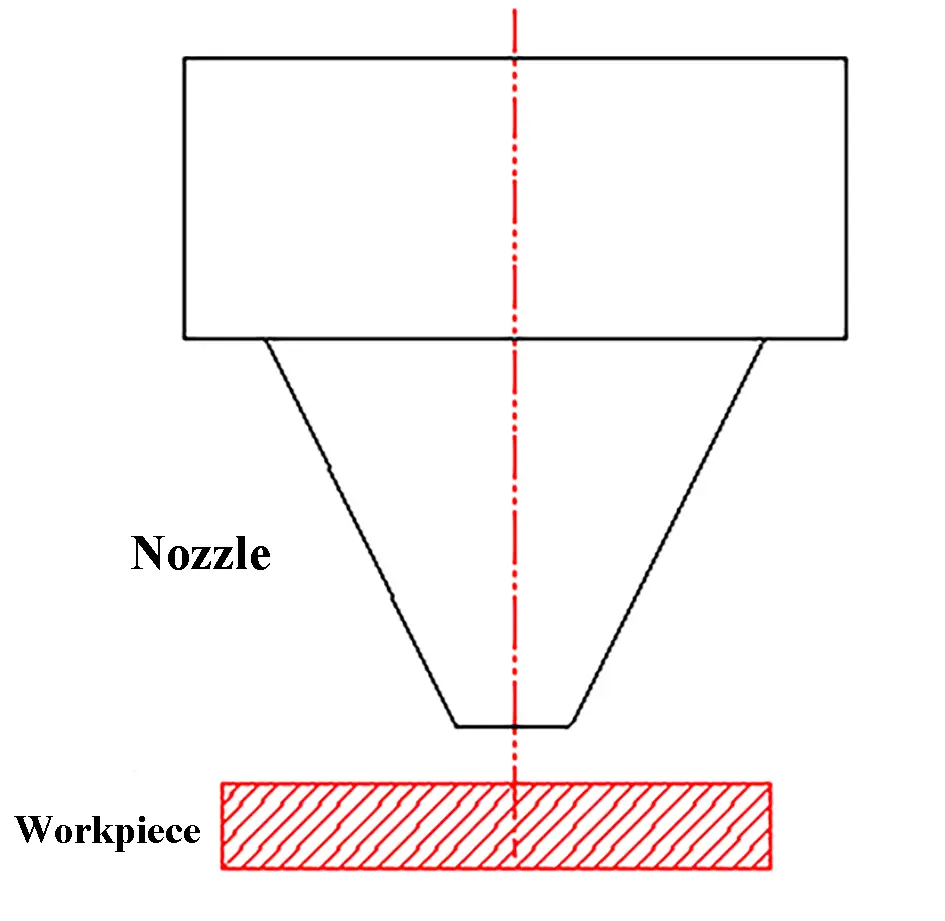
Fig. 15 Altura do bico
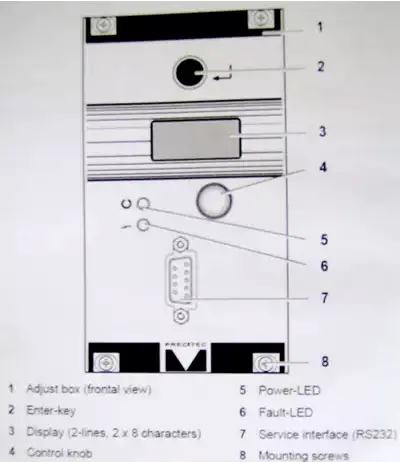
Caixa de controle de sensor capacitivo
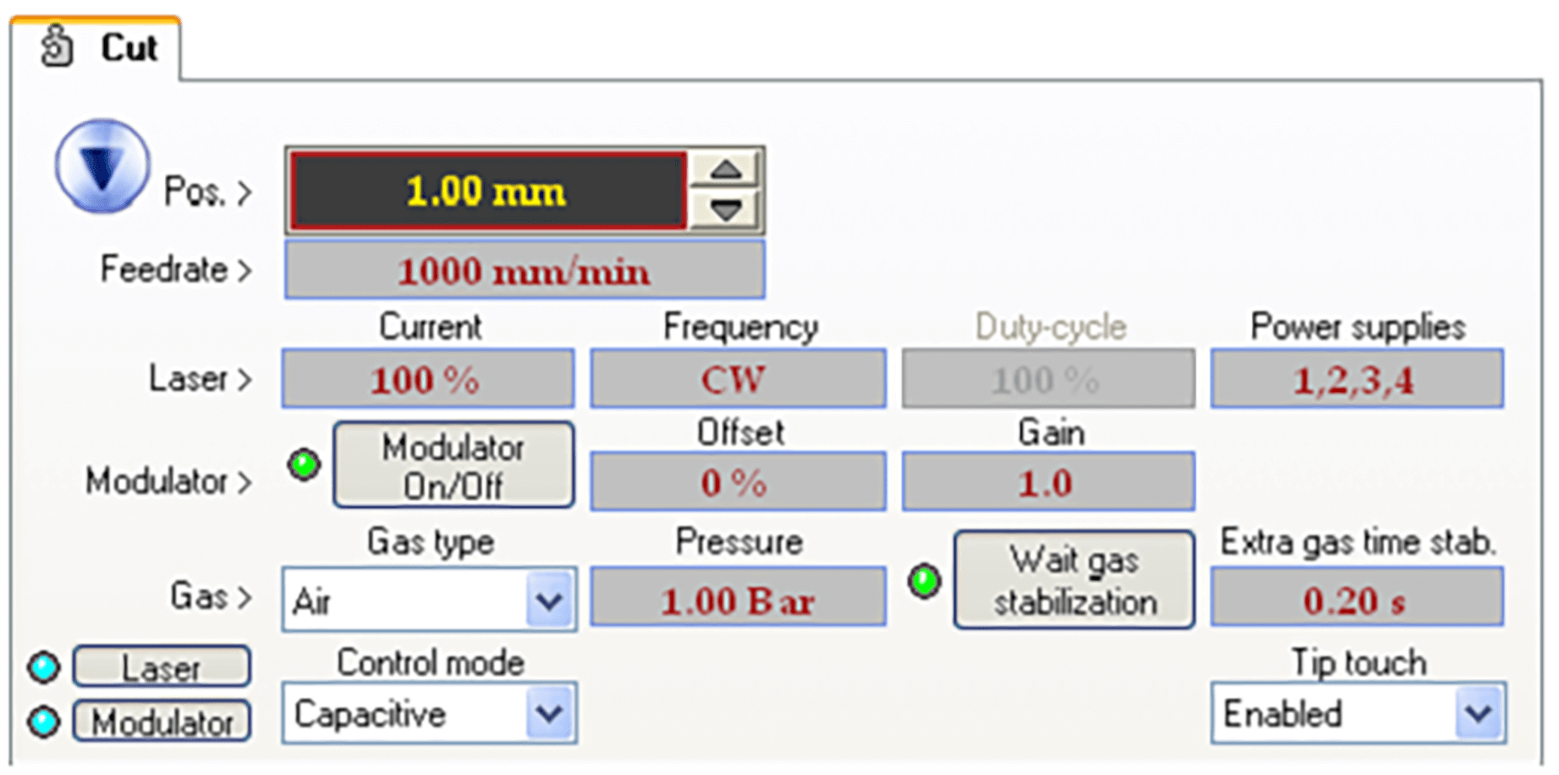
Como mostrado na figura o item de ajuste de altura do bico é mostrado.
4. Velocidade de corte
A velocidade de corte tem impacto direto na largura e rugosidade da incisão. Existe um valor ideal para a velocidade de corte que varia com a espessura do material e a pressão do gás de corte. Este valor normalmente fica em torno de 80% da velocidade máxima de corte.
1. Velocidade muito rápida
Se a velocidade de corte for muito alta, poderá causar os seguintes problemas:
- Cortes incompletos com faíscas aleatórias.
- Cortes inconsistentes com algumas áreas cortadas e outras não.
- Uma seção de corte grosso sem solução.
A seção cortada terá estrias inclinadas e manchas de solução na parte inferior.
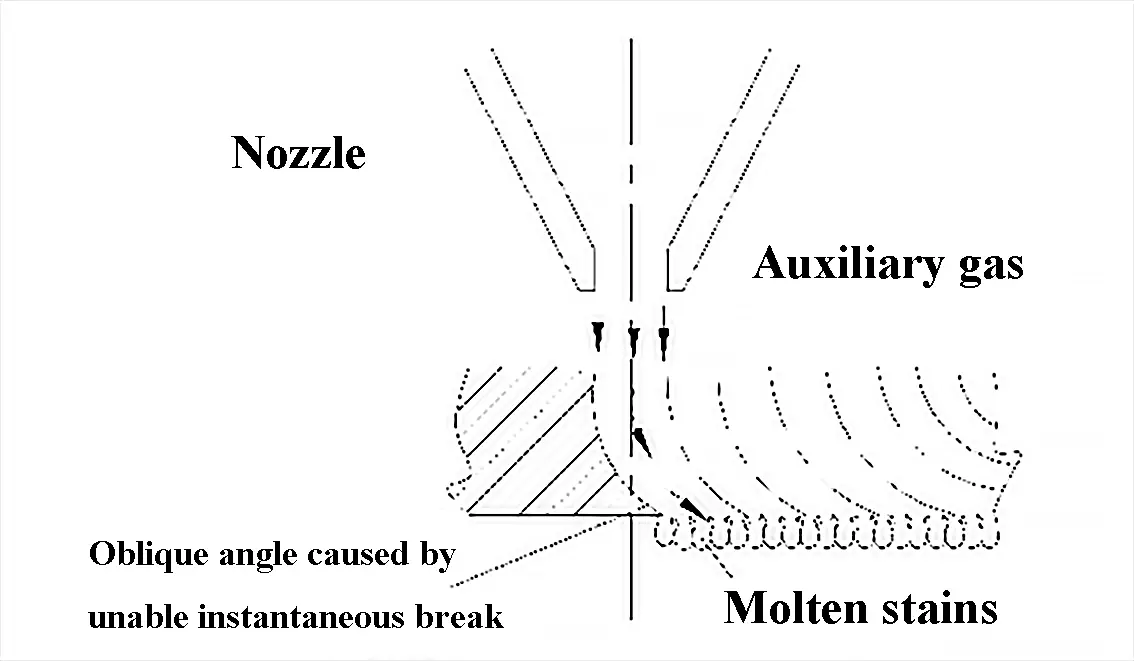
Fig. 18 Velocidade muito rápida
2. Velocidade muito lenta
(1) A fusão excessiva leva a uma superfície de corte áspera.
(2) A fenda se alarga e os cantos afiados derretem.
(3) Isto impacta a eficiência de corte.
3. Determine a velocidade de corte apropriada
Determinar se deve aumentar ou diminuir a velocidade de avanço com base nas faíscas de corte.
1) Faíscas se espalham de cima para baixo
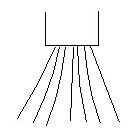
Fig. 19 Velocidade normal de corte
2) Se a faísca estiver inclinada, a velocidade de corte é muito rápida.
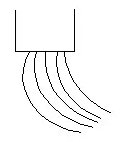
Fig. 20 Velocidade de corte muito rápida
3) Se as faíscas não forem difusas e forem poucas, e se juntarem, a velocidade é muito lenta.
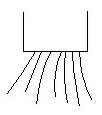
Fig. 21 Velocidade de corte muito lenta
A velocidade de alimentação é adequada.
Conforme ilustrado na figura, a superfície de corte apresenta uma linha relativamente suave e não há derretimento na metade inferior.
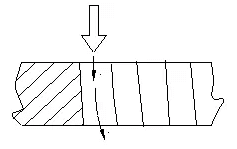
Fig. 22 Velocidade normal de corte
V. Corte de gás auxiliar
Considere os seguintes fatores ao selecionar o tipo e a pressão do gás auxiliar de corte:
- O oxigênio é normalmente usado para cortar aço carbono comum com perfuração e corte de baixa pressão.
- O corte a ar é comumente usado para corte de não metais.
- O nitrogênio é geralmente usado para cortar aço inoxidável.
- A qualidade do corte melhora com maior pureza do gás.
- Para corte de chapas de aço de baixo carbono, a pureza do gás deve ser de pelo menos 99,6%, e para corte de chapas de aço carbono com espessura superior a 12 mm, a pureza do oxigênio deve ser superior a 99,9%.
- A pureza do nitrogênio para corte de chapas de aço inoxidável deve estar acima de 99,6%.
- Uma maior pureza de nitrogênio resulta em cortes de melhor qualidade.
- A baixa pureza do gás não afeta apenas a qualidade do corte, mas também causa contaminação da lente.
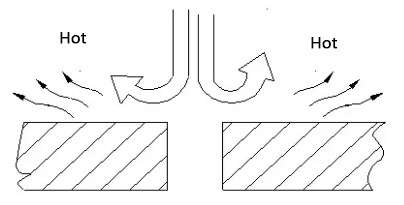
1. A influência do gás auxiliar na qualidade do corte
(1) O gás contribui para a dissipação de calor e combustão, remove a solução e melhora a qualidade da superfície de corte.
(2) Os efeitos da baixa pressão do gás no corte.
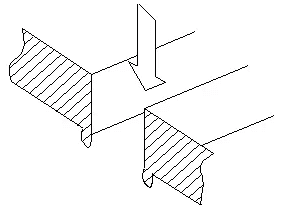
a. A superfície de corte derreteu.
b. A velocidade de corte não pode ser aumentada, afetando a eficiência.
(3) A influência da alta pressão do gás na qualidade do corte
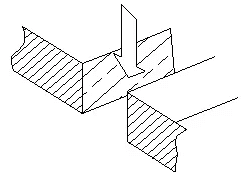
a. Se o fluxo de ar for muito alto, a superfície de corte será mais espessa e a costura será mais larga.
b. Se o fluxo de ar for excessivo, a peça cortada derreterá e não será possível obter uma boa qualidade de corte.
2. O efeito do gás auxiliar na perfuração
(1) Quando a pressão do gás é muito baixa, fica difícil penetrar e o tempo aumenta.
(2) Quando a pressão do gás é muito alta, o ponto de penetração derrete e uma grande área de fusão é formada.
Como resultado, a pressão de perfuração para chapas finas é maior do que para chapas grossas.
3. Gás auxiliar para corte de plexiglass
Plexiglass é inflamável. Para obter uma superfície de corte transparente e brilhante, o nitrogênio ou o ar são escolhidos como retardadores de chama. Se o oxigênio for selecionado, a qualidade do corte não será boa o suficiente. Portanto, é necessário selecionar a pressão apropriada com base na situação real durante o corte.
Quanto menor for a pressão do gás, maior será o brilho da luz de corte e mais estreita será a secção do cabelo. No entanto, se a pressão do gás for muito baixa, resultará em velocidade de corte lenta e chama sob a superfície da placa, o que pode impactar negativamente a qualidade da superfície inferior.
VI. Potência laser
A potência do laser necessária para o corte a laser depende principalmente do tipo de corte e das propriedades do material a ser cortado. O maior requisito de potência do laser é para corte por vaporização, seguido por corte por fusão e corte por oxigênio.
A potência do laser tem um impacto significativo na espessura do corte, velocidade e largura da incisão. À medida que a potência do laser aumenta, a espessura do material que pode ser cortado aumenta, a velocidade de corte acelera e a largura da incisão também aumenta.
A potência do laser desempenha um papel crucial na determinação do processo e da qualidade do corte.
1. A energia é muito pequena para cortar
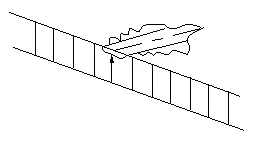
Fig. 26 Potência muito baixa
2. Se a potência for muito alta, toda a superfície de corte derreterá.
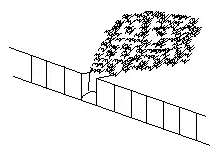
Fig. 27 Potência excessiva
3. A energia é insuficiente, resultando em manchas derretidas após o corte.
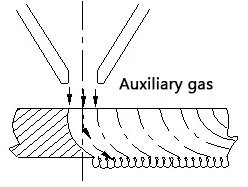
Fig. 28 Deficiência de energia
4. A potência é apropriada, a superfície de corte é boa sem manchas derretidas.
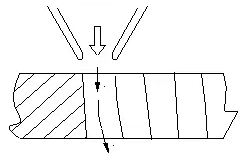
Fig. 29 Potência adequada
Resumo dos parâmetros de corte
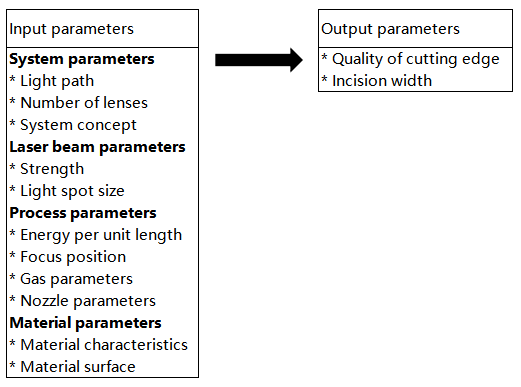
Os principais parâmetros do corte a laser
Velocidade de corte
Dada a densidade de potência do laser e o material, a velocidade de corte segue uma fórmula empírica. Desde que esteja acima do limite, a velocidade de corte do material é proporcional à potência do laser, o que significa que aumentar a densidade de potência pode aumentar a velocidade de corte.
A velocidade de corte também é inversamente proporcional à densidade e espessura do material a ser cortado. Existem várias maneiras de melhorar a velocidade de corte:
(1) Aumentar a potência (na faixa de 500-3000W);
(2) Alterar o modo de feixe;
(3) Reduza o tamanho do ponto de foco (por exemplo, usando uma lente de distância focal curta).
Para materiais metálicos, se outras variáveis do processo permanecerem inalteradas, a velocidade de corte a laser pode ser ajustada dentro de uma faixa, mantendo ao mesmo tempo uma qualidade de corte satisfatória. Esta faixa parece ser relativamente ampla ao cortar metais finos.
Posição de foco
Depois que o feixe de laser é focado, o tamanho do ponto é proporcional à distância focal da lente. Uma lente de distância focal curta resulta em um tamanho de ponto pequeno e alta densidade de potência no ponto focal, tornando-a ideal para corte de material. No entanto, suas desvantagens são uma profundidade de foco muito curta e uma margem de ajuste limitada, tornando-a normalmente adequada para corte em alta velocidade de materiais finos.
Para peças mais espessas, uma lente telefoto com maior profundidade focal é mais adequada para corte, desde que tenha densidade de potência suficiente.
Na maioria dos casos, a densidade de potência mais alta está no ponto focal, que geralmente fica logo na superfície ou ligeiramente abaixo da superfície da peça durante o corte. Manter uma posição relativa constante entre o ponto focal e a peça é crucial para obter uma qualidade de corte estável.
É importante observar que durante a operação, a lente pode aquecer devido ao resfriamento insuficiente, fazendo com que a distância focal mude. Nesses casos, é necessário ajustar a posição focal em tempo hábil.
Gás auxiliar
O gás auxiliar é pulverizado ao longo do mesmo eixo do feixe de laser para proteger a lente contra contaminação e remover a escória fundida na parte inferior da área de corte. Para materiais não metálicos e alguns materiais metálicos, é utilizado ar comprimido ou um gás inerte para remover os materiais fundidos e evaporados e evitar combustão excessiva na área de corte.
Pressão de gás auxiliar
A maior parte do corte a laser de metal usa um gás reativo (oxigênio) para criar uma reação exotérmica oxidativa com o metal quente. Este calor adicional pode aumentar a velocidade de corte em 1/3 a 1/2.
Ao cortar chapas finas em altas velocidades, é necessária uma pressão de gás mais alta para evitar que a parte posterior do corte adira à escória. Ao cortar materiais mais espessos ou em velocidades mais lentas, a pressão do gás pode ser reduzida conforme apropriado.
Potência de saída do laser
A potência do laser e a qualidade do modo terão um impacto significativo no corte. Na operação real, a potência máxima é frequentemente definida para atingir uma alta velocidade de corte ou para cortar materiais espessos.
Embrulhe isso
O parágrafo acima descreve a maioria dos fatores que podem impactar os parâmetros do efeito de corte. A tabela a seguir lista valores típicos para parâmetros de corte. Estes valores não são específicos de nenhum caso particular, mas podem ser usados como referência para determinar os parâmetros de partida corretos.
Valores típicos dos parâmetros de corte do aço inoxidável DC030
Grossura (milímetros) |
Comprimento focal (polegada) |
Posição de foco (milímetros) |
Potência laser (C) |
Velocidade de corte (m/min) |
Pressão do gás N2(barra) |
Diâmetro do bico (milímetros) |
Distância do bico à placa (milímetros) |
---|---|---|---|---|---|---|---|
1 | 5 | -0,5 | 3.000 | 28 | 10 | 1,5 | 0,5 |
2 | 5 | -1 | 3.000 | 8 | 10 | 1,5 | 0,5 |
3 | 5 | -2 | 3.000 | 4,75 | 15 | 1,5 | 0,5 |
4 | 7,5 | -3 | 3.000 | 3.8 | 17,5 | 2 | 0,7 |
5 | 7,5 | -4 | 3.000 | 2.2 | 20 | 2 | 0,7 |
6 | 10 | -5 | 3.000 | 2 | 20 | 2.2 | 0,7 |
8 | 12,5/15 | -6 | 3.000 | 13 | 20 | 3 | 0,7 |
10 | 15 | -6 | 3.000 | 0,55 | 20 | 3 | 0,7 |
Valores típicos dos parâmetros de corte de aço de baixo carbono DC030
Grossura (milímetros) |
Comprimento focal (polegada) |
Posição de foco (milímetros) |
Potência laser (C) |
Velocidade de corte (m/min) |
Pressão do gás O2(barra) |
Diâmetro do bico (milímetros) |
Distância do bico à placa (milímetros) |
---|---|---|---|---|---|---|---|
1 | 5 | 0 | 750 | 9 | 3.5 | 1 | 0,5 |
2 | 5 | -0,5 | 800 | 7 | 3 | 1 | 1 |
3 | 5 | -0,5 | 800 | 4 | 3 | 1 | 1 |
4 | 7,5 | 2 | 3.000 | 4.2 | 0,7 | 1 | 1 |
6 | 7,5 | 2 | 3.000 | 3.3 | 0,7 | 1.2 | 1 |
8 | 7,5 | 2 | 3.000 | 2.3 | 0,7 | 1,5 | 1 |
10 | 7,5 | 2 | 3.000 | 1,8 | 0,7 | 1,5 | 1 |
12 | 7,5 | 2 | 3.000 | 1,5 | 0,7 | 1,5 | 1 |
15 | 7,5 | 2 | 3.000 | 1.1 | 0,7 | 2 | 1 |
20 | 7,5 | 2,5 | 3.000 | 0,7 | 0,7 | 2.4 | 1 |
Valores típicos dos parâmetros de corte do aço DC025A1Mg3N2
Grossura (milímetros) |
Comprimento focal (polegada) |
Posição de foco (milímetros) |
Potência laser (C) |
Velocidade de corte (m/min) |
Pressão do gás O2(barra) |
Diâmetro do bico (milímetros) |
Distância do bico à placa (milímetros) |
---|---|---|---|---|---|---|---|
2 | 7,5 | -2,5 | 2500 | 45-6,5 | 10-12 | 1,5 | ≥1,0 |
3 | 7,5 | -3,5 | 2500 | 3,0-4,0 | 12-15 | 1,5 | ≥1,0 |
4 | 7,5 | -5,0 | 2500 | 1,5-2,0 | 12-16 | 2,0 | ≥1,0 |
5 | 7,5 | -5,0 | 2500 | 0,9-1,0 | 12-16 | 2,0 | ≥1,0 |
As fotos a seguir mostram o corte de chapas de aço carbono de 15mm e aço inoxidável de 8mm em diferentes distâncias focais.
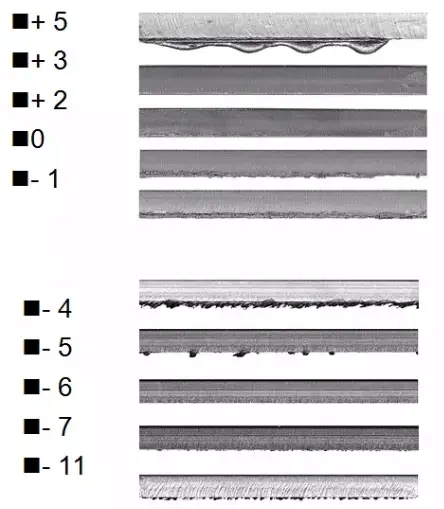